HRB500 reinforcing steel bar and preparation method thereof
A technology of steel bar and chemical composition, applied in the production field of low alloy steel, can solve the problems of large fluctuation of steel performance, high welding performance, high content of ⅰ silicon manganese and carbon, reduce eutectoid transformation temperature, delay pearlite transformation, The effect of improving the strength of steel bars
- Summary
- Abstract
- Description
- Claims
- Application Information
AI Technical Summary
Problems solved by technology
Method used
Image
Examples
Embodiment 1
[0034] According to the weight percentage of chemical composition C: 0.15%, Si: 0.49%, Mn: 1.5%, P: 0.025%, S: 0.015%, B: 0.0024%, the raw materials are weighed, desulfurized by molten iron, converter smelting, deoxidation outside the furnace, blowing Argon, billet protection pouring, billet heating, rolling, controlled cooling after rolling, cooling bed air cooling, cutting to length, bundling and storage to obtain HRB500 steel bars; among them:
[0035] 1) In the billet protection pouring process, the superheat of molten steel is controlled to 35°C, a magnesium tundish is used, the penetration depth of the tundish nozzle is 120mm; the billet casting speed is 1.2m / min, and the casting billet continuous casting straightening temperature is 950°C;
[0036] 2) During billet heating: heat the billet to 1150°C in the furnace and keep it for 120 minutes;
[0037] 3) During the rolling process: the rolling start temperature is 1050°C, the rolling pass is 2 billet opening passes, the...
Embodiment 2
[0040] According to the weight percentage of chemical composition C: 0.13%, Si: 0.45%, Mn: 1.35%, P: 0.028%, S: 0.018%, B: 0.0019%, the raw materials are weighed, desulfurized by molten iron, converter smelting, deoxidation outside the furnace, blowing Argon, billet protection pouring, billet heating, rolling, controlled cooling after rolling, cooling bed air cooling, cutting to length, bundling and storage to obtain HRB500 steel bars; among them:
[0041] 1) In the billet protection pouring process, the superheat of molten steel is controlled to 15°C, a magnesium tundish is used, and the penetration depth of the tundish nozzle is 120mm; the casting speed is 1.5m / min, and the continuous casting and straightening temperature of the cast slab is 1000°C;
[0042] 2) During the billet heating process: heat the billet to 1250°C in the furnace for 100 minutes;
[0043] 3) During the rolling process: the rolling start temperature is 1150°C, the rolling pass is 2 for billet opening, 1...
Embodiment 3
[0046] According to the weight percentage of chemical composition C: 0.15%, Si: 0.6%, Mn: 1.6%, P: 0.023%, S: 0.028%, B: 0.004%, the raw materials are weighed, desulfurized by molten iron, converter smelting, deoxidation outside the furnace, blowing Argon, billet protection pouring, billet heating, rolling, controlled cooling after rolling, cooling bed air cooling, cutting to length, bundling and storage to obtain HRB500 steel bars; among them:
[0047] 1) During the billet protection pouring process, the superheat of molten steel is controlled to 20°C, a magnesium tundish is used, and the penetration depth of the tundish nozzle is 130mm; the billet casting speed is 1.4m / min, and the casting billet continuous casting straightening temperature is 980°C;
[0048] 2) During billet heating: heat the billet in the furnace to 1200°C for 100 minutes;
[0049] 3) During the rolling process: the rolling start temperature is 1050°C, the rolling pass is 2 passes, and the rough rolling is...
PUM
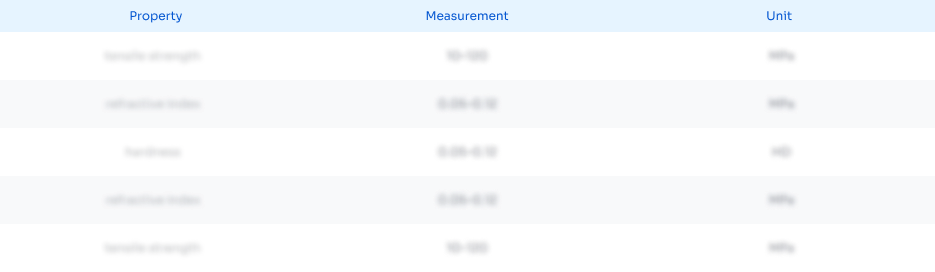
Abstract
Description
Claims
Application Information

- R&D
- Intellectual Property
- Life Sciences
- Materials
- Tech Scout
- Unparalleled Data Quality
- Higher Quality Content
- 60% Fewer Hallucinations
Browse by: Latest US Patents, China's latest patents, Technical Efficacy Thesaurus, Application Domain, Technology Topic, Popular Technical Reports.
© 2025 PatSnap. All rights reserved.Legal|Privacy policy|Modern Slavery Act Transparency Statement|Sitemap|About US| Contact US: help@patsnap.com