Dispensing device container filled with liquid curable composition, manufacturing method thereof, and dispensing device
A technology of curable composition and manufacturing method, which is applied in the fields of devices for coating liquid on the surface, semiconductor/solid-state device manufacturing, lighting devices, etc., and can solve problems such as the influence of liquid curable composition properties, generation of bubbles, and increase in viscosity , to achieve excellent storage stability and prevent air bubbles
- Summary
- Abstract
- Description
- Claims
- Application Information
AI Technical Summary
Problems solved by technology
Method used
Image
Examples
Embodiment
[0416] The present invention will be described in more detail below with reference to specific examples, but the present invention is not limited to the following examples.
[0417] In addition, in the following examples, "number average molecular weight" and "molecular weight distribution (ratio of weight average molecular weight to number average molecular weight)" were calculated by the standard polystyrene conversion method using gel permeation chromatography (GPC). However, a column packed with polystyrene cross-linked gel was used as a GPC column (shodex GPC K-804 and K-802.5; manufactured by Showa Denko Co., Ltd.), and chloroform was used as a GPC solvent.
[0418] 1 ASX-400 (400 MHz) manufactured by Bruker Co., Ltd. was used for H-NMR, and it measured at 23 degreeC using heavy chloroform as a solvent.
[0419] In the following examples, the "average number of terminal crosslinkable silyl groups or (meth)acryloyl groups" is "the number of crosslinkable silyl groups and...
manufacture example 1、2
[0423] The amount of each raw material used is shown in Table 1.
[0424] (1) Polymerization process
[0425] Acrylates (premixed acrylates) were deoxygenated. The inside of the stainless steel reaction container with a stirrer was deoxidized, and part of cuprous bromide and all acrylates (in Table 1, the monomer charged initially) was charged, and heated and stirred. Add and mix acetonitrile (recorded as acetonitrile for polymerization in Table 1), diethyl 2,5-dibromoadipate (DBAE) or ethyl 2-bromobutyrate as initiator, at the temperature of the mixture When the temperature was adjusted to about 80° C., pentamethyldiethylenetriamine (hereinafter, simply referred to as triamine) was added to start the polymerization reaction. The remaining acrylates (referred to as additional monomers in Table 1) were gradually added to perform a polymerization reaction. During the polymerization, a triamine is appropriately added to adjust the polymerization rate. The total amount of tria...
manufacture example 3
[0440] The amount of each raw material used is shown in Table 2.
[0441] (1) Polymerization process
[0442] Deoxygenation of acrylates (in the case of copolymerization, premixed with a given amount of acrylates) is carried out. The inside of the stainless steel reaction container with a stirrer was deoxidized, and part of cuprous bromide and all acrylates (in Table 2, the monomer charged initially) was charged, and heated and stirred. Add and mix acetonitrile (referred to as acetonitrile for polymerization in Table 2), diethyl 2,5-dibromoadipate (DBAE) as an initiator, and add pentaform when the temperature of the mixture is adjusted to about 80°C Diethylenetriamine (hereinafter referred to simply as triamine) to start the polymerization reaction. The remaining acrylate (referred to as an additional monomer in Table 2) was gradually added to perform polymerization reaction. During the polymerization, a triamine is appropriately added to adjust the polymerization rate. The ...
PUM
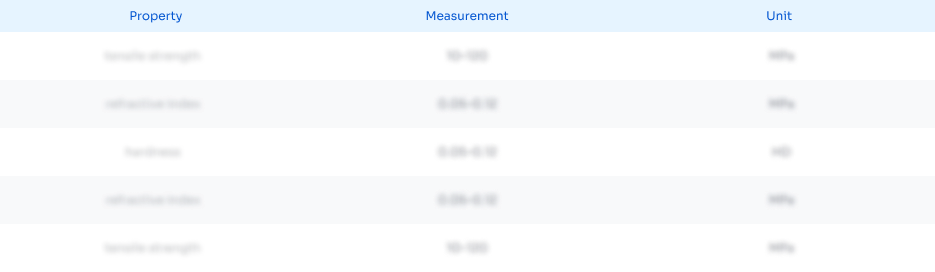
Abstract
Description
Claims
Application Information

- R&D Engineer
- R&D Manager
- IP Professional
- Industry Leading Data Capabilities
- Powerful AI technology
- Patent DNA Extraction
Browse by: Latest US Patents, China's latest patents, Technical Efficacy Thesaurus, Application Domain, Technology Topic, Popular Technical Reports.
© 2024 PatSnap. All rights reserved.Legal|Privacy policy|Modern Slavery Act Transparency Statement|Sitemap|About US| Contact US: help@patsnap.com