Polyvinyl chloride soft foam plastic coiled material and preparation method thereof
A technology of flexible foam plastics and polyethylene, applied in the field of chemical materials, can solve problems such as brittleness, decreased toughness, and shortened service life, and achieve the effects of good permeability resistance, good performance, and good flexibility
- Summary
- Abstract
- Description
- Claims
- Application Information
AI Technical Summary
Problems solved by technology
Method used
Image
Examples
Embodiment 1
[0016] A polyethylene flexible foam plastic coil, comprising: 80 parts of low-density polyethylene resin, 1 part of zinc oxide, 10 parts of azodicarbonamide, 0.5 part of dicumyl peroxide, tetrabromo 0.5 parts of ethane, 0.5 parts of zinc stearate, 1 part of glycerin, 0.2 parts of benzophenone, and 1 part of p-isocyanate.
[0017] The preparation method of the above-mentioned flexible polyethylene foam coil is prepared according to the following steps:
[0018] (1) Weigh each component according to parts by weight;
[0019] (2) Stir and mix each component in a mixer, where the stirring temperature is 50°C, the stirring speed is 70 rpm, and the stirring time is 20 minutes;
[0020] (3) Granulate the mixed material on a mixing and granulating machine, where the mixing temperature is 110°C;
[0021] (4) After the mixing is finished, cut into pellets on the pelletizer, and then carry out extrusion and calendering;
[0022] (5) Foaming, washing and drying after calendering, coili...
Embodiment 2
[0024] A polyethylene flexible foamed plastic coil, comprising by weight components: 84 parts of low-density polyethylene resin, 2 parts of zinc oxide, 12 parts of azodicarbonamide, 0.6 part of dicumyl peroxide, tetrabromo 0.6 parts of ethane, 0.8 parts of zinc stearate, 2 parts of glycerin, 0.3 parts of benzophenone, and 2 parts of p-isocyanate.
[0025] The preparation method of the above-mentioned flexible polyethylene foam coil is prepared according to the following steps:
[0026] (1) Weigh each component according to parts by weight;
[0027] (2) Stir and mix each component in a mixer, where the stirring temperature is 52°C, the stirring speed is 75 rpm, and the stirring time is 20 minutes;
[0028] (3) Granulate the mixed material on a mixing and granulating machine, where the mixing temperature is 115°C;
[0029] (4) After the mixing is finished, cut into pellets on the pelletizer, and then carry out extrusion and calendering;
[0030] (5) Foaming, washing and dryin...
Embodiment 3
[0032] A polyethylene flexible foam plastic coil, comprising: 85 parts of low-density polyethylene resin, 3 parts of zinc oxide, 13 parts of azodicarbonamide, 0.8 part of dicumyl peroxide, tetrabromo 0.7 parts of ethane, 1.3 parts of zinc stearate, 3 parts of glycerin, 0.4 parts of benzophenone, and 3 parts of p-isocyanate.
[0033] The preparation method of the above-mentioned flexible polyethylene foam coil is prepared according to the following steps:
[0034] (1) Weigh each component according to parts by weight;
[0035] (2) Stir and mix each component in a mixer, where the stirring temperature is 55°C, the stirring speed is 75 rpm, and the stirring time is 25 minutes;
[0036] (3) Granulate the mixed material on a mixing and granulating machine, where the mixing temperature is 118°C;
[0037] (4) After the mixing is finished, cut into pellets on the pelletizer, and then carry out extrusion and calendering;
[0038] (5) Foaming, washing and drying after calendering, co...
PUM
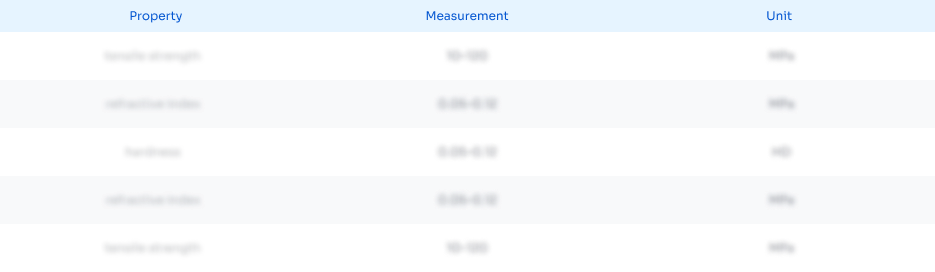
Abstract
Description
Claims
Application Information

- R&D
- Intellectual Property
- Life Sciences
- Materials
- Tech Scout
- Unparalleled Data Quality
- Higher Quality Content
- 60% Fewer Hallucinations
Browse by: Latest US Patents, China's latest patents, Technical Efficacy Thesaurus, Application Domain, Technology Topic, Popular Technical Reports.
© 2025 PatSnap. All rights reserved.Legal|Privacy policy|Modern Slavery Act Transparency Statement|Sitemap|About US| Contact US: help@patsnap.com