Method for preparing nano-scale ZSM-5 molecular sieve by using coal ash
A technology of ZSM-5 and fly ash, which is applied in the direction of nanotechnology, nanotechnology, nanotechnology, etc. for materials and surface science, can solve the problem of high production cost of ZSM-5 molecular sieve, and achieve high-value utilization, Lower synthesis cost and better crystallinity
- Summary
- Abstract
- Description
- Claims
- Application Information
AI Technical Summary
Problems solved by technology
Method used
Image
Examples
Embodiment 1
[0025] combine figure 2 , take fly ash collected on site as raw material, grind it into fine powder, pass through a 200-mesh sieve, take 100g of fine powder and place it in a muffle furnace, calcinate at 800°C for 2 hours, then burn it at a temperature of 75°C and a speed of 250r / Min was washed twice with water for 0.5 hours each time, and then the washing liquid was separated from the fly ash for solid-liquid separation. After separation, the solid was dried at 120°C for 5 hours for later use; the pretreated fly ash was mixed with Na 2 CO 3 The mass ratio of solids is 1:1 and mixed evenly. After roasting at 800°C for 2 hours, take it out and cool it to 25°C for later use; then impregnate the roasted product with 3mol / L HCl for 60 minutes, filter to remove insoluble matter, and obtain silica-rich gel and crude AlCl 3 solution. Adjust crude AlCl with 4% NaOH 3 pH value of the solution to 3.5, filtered to remove Fe(OH) 3 , the filtrate continued to add NaOH dropwise until...
Embodiment 2
[0027] Use fly ash collected on site as raw material, grind it into fine powder, pass through a 200-mesh sieve, put 100g of fine powder in a muffle furnace, calcinate at 750°C for 3 hours, then wash with water at 50°C and 200r / min for 2 hours time, 1 hour each time, and then carry out solid-liquid separation between the washing solution and the fly ash, and dry the solid at 120°C for 5 hours after separation; the pretreated fly ash and Na 2 CO 3 The mass ratio of solids is 1:1.2 and mixed evenly. After roasting at 750°C for 2.5 hours, take it out and cool it to 25°C for later use; then impregnate the roasted product with 2.5mol / L HCl for 70 minutes, filter to remove insoluble matter, and obtain silicon-rich gel and Crude AlCl 3 solution. Adjust crude AlCl with 8% NaOH 3 pH value of the solution to 3, filtered to remove Fe(OH) 3 , the filtrate continued to add NaOH dropwise until the precipitation in the filtrate no longer increased, and the Mg(OH) was removed by filtration...
Embodiment 3
[0029] Use fly ash collected on site as raw material, grind it into fine powder, pass through a 200-mesh sieve, put 100g of fine powder in a muffle furnace, calcinate at 750°C for 3 hours, then wash with water at 50°C and 200r / min for 2 hours time, 1 hour each time, and then carry out solid-liquid separation between the washing solution and the fly ash, and dry the solid at 120°C for 5 hours after separation; the pretreated fly ash and Na 2 CO 3 The mass ratio of solids is 1:1.2 and mixed evenly. After roasting at 750°C for 2.5 hours, take it out and cool it to 25°C for later use; then impregnate the roasted product with 2.5mol / L HCl for 70 minutes, filter to remove insoluble matter, and obtain silicon-rich gel and Crude AlCl 3 solution. Adjust crude AlCl with 8% NaOH 3 pH value of the solution to 3, filtered to remove Fe(OH) 3 , the filtrate continued to add NaOH dropwise until the precipitation in the filtrate no longer increased, and the Mg(OH) was removed by filtration...
PUM
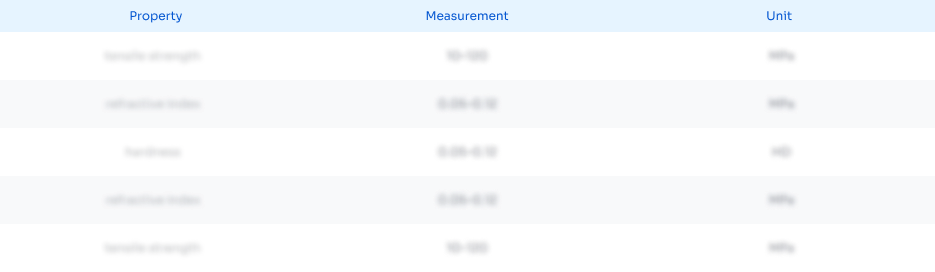
Abstract
Description
Claims
Application Information

- R&D Engineer
- R&D Manager
- IP Professional
- Industry Leading Data Capabilities
- Powerful AI technology
- Patent DNA Extraction
Browse by: Latest US Patents, China's latest patents, Technical Efficacy Thesaurus, Application Domain, Technology Topic, Popular Technical Reports.
© 2024 PatSnap. All rights reserved.Legal|Privacy policy|Modern Slavery Act Transparency Statement|Sitemap|About US| Contact US: help@patsnap.com