Current-assisted rapid hot forming device and method for long and thin high-strength-steel structural components
A technology for structural parts and high-strength steel, which is applied in the field of current-assisted self-resistance heating forming devices, can solve the problems of complicated electrification, high hardness and high melting point, and achieve the effects of uniform temperature distribution, uniform temperature, convenient and firm support
- Summary
- Abstract
- Description
- Claims
- Application Information
AI Technical Summary
Problems solved by technology
Method used
Image
Examples
specific Embodiment approach 1
[0019] Specific implementation mode one: see figure 1 and figure 2 Describe this embodiment, the current-assisted rapid hot forming device for high-strength steel slender structural parts described in this embodiment, it includes a power supply 1, a mold, a pair of sheet metal clamping electrodes 3, two spacers 4 and two insulating mica piece 5,
[0020] Described mold is made up of upper mold 2-1 and lower mold 2-2,
[0021] Two pads 4 are respectively located on both sides of the lower mold 2-2, and a pad 4 and a plate holding electrode 3 are fixedly connected by an insulating mica sheet 5,
[0022] The upper mold 2-1 is located directly above the sheet material 6 to be formed, the lower mold 2-2 is located directly below the sheet material 6 to be formed, and the forming part of the sheet material 6 to be formed is placed in the cavity of the lower mold. The holding electrode 3 is used to clamp the sheet to be formed, and the two electrode ends of the sheet holding elec...
specific Embodiment approach 2
[0025] Embodiment 2: This implementation method is a further limitation of Embodiment 1. It also includes an infrared thermometer, which is used to measure the temperature of the sheet 6 to be formed in real time.
specific Embodiment approach 3
[0026] Embodiment 3: This implementation method is a further limitation of Embodiment 1. The plate holding electrode 3 is a holding member composed of two copper plates.
PUM
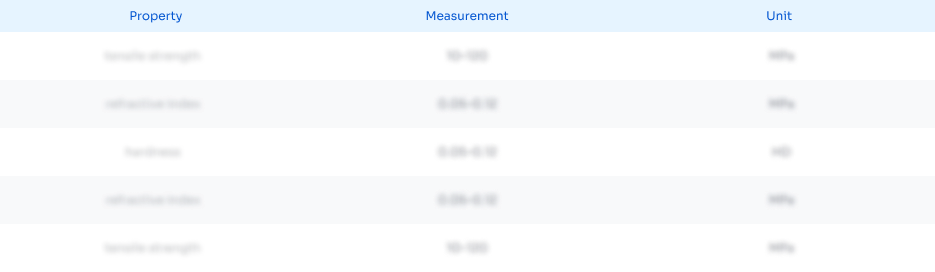
Abstract
Description
Claims
Application Information

- Generate Ideas
- Intellectual Property
- Life Sciences
- Materials
- Tech Scout
- Unparalleled Data Quality
- Higher Quality Content
- 60% Fewer Hallucinations
Browse by: Latest US Patents, China's latest patents, Technical Efficacy Thesaurus, Application Domain, Technology Topic, Popular Technical Reports.
© 2025 PatSnap. All rights reserved.Legal|Privacy policy|Modern Slavery Act Transparency Statement|Sitemap|About US| Contact US: help@patsnap.com