Beneficiation method for recycling bismuth from molybdenum selecting tailings
A beneficiation method and technology for molybdenum tailings, which are applied in flotation, solid separation and other directions, can solve the problems of poor activation of bismuthite and low recovery rate, and achieve low beneficiation cost, improved flotation recovery rate, and simple process flow. Effect
- Summary
- Abstract
- Description
- Claims
- Application Information
AI Technical Summary
Problems solved by technology
Method used
Image
Examples
Embodiment 1
[0016] The molybdenum tailings of a mine in Jiangxi contain Bi 2.54%, Mo 0.0027%, and S 13.69%.
[0017] Slurry preparation: add sulfuric acid to adjust the pH value of the slurry to 5.5, and stir for 10 minutes; perform primary flotation roughing on molybdenum tailings according to the amount of chemicals listed in Table 1, secondary flotation sweeping, and three blank separations to obtain bismuth Concentrates and flotation tailings. The bismuth recovery rate is 97.81%, and the bismuth concentrate contains 33.64% Bi.
[0018] The results of Example 1 are shown in Table 2.
[0019] The result of table 2 embodiment 1
[0020] name Yield(%) Bismuth content (%) Bismuth recovery rate (%) Bismuth concentrate 7.38 33.64 97.81 Flotation tailings 92.62 0.06 2.19 Molybdenum tailings 100.00 2.54 100.00
Embodiment 2
[0022] The molybdenum tailings of a polymetallic mine in Hunan contain 0.27% Bi, 0.0014% Mo and 6.77% S.
[0023] Slurry adjustment: add sulfuric acid to adjust the pH value of the slurry to 6, and stir for 15 minutes; carry out one flotation roughing, one flotation sweep and one blank sweep, and four blank Concentrate to obtain bismuth concentrate and flotation tailings. The recovery rate of bismuth was 86.19%. Bismuth concentrate contains 21.33% Bi.
[0024] The results of Example 2 are shown in Table 3.
[0025] The result of table 3 embodiment 2
[0026] name Yield(%) Bismuth content (%) Bismuth recovery rate (%) Bismuth concentrate 1.10 21.33 86.19 Flotation tailings 98.90 0.038 13.81 Molybdenum tailings 100.00 0.27 100.00
Embodiment 3
[0028] The molybdenum tailings of a molybdenum mine in Henan contain 0.41% Bi, 0.0030% Mo and 9.71% S.
[0029] Slurry adjustment: add sulfuric acid to adjust the pH value of the slurry to 6, and stir for 15 minutes; carry out a flotation roughing on the molybdenum tailings according to the amount of chemicals listed in Table 1, a second flotation sweep, and 4 blank selections to obtain Bismuth concentrate and flotation tailings. The bismuth recovery rate is 88.81%, and the bismuth concentrate contains 24.16% Bi.
[0030] The results of Example 3 are shown in Table 4.
[0031] The result of table 4 embodiment 3
[0032] name Yield(%) Bismuth content (%) Bismuth recovery rate (%) Bismuth concentrate 1.52 24.16 88.81 Flotation tailings 98.48 0.047 11.19 Molybdenum tailings 100.00 0.41 100.00
PUM
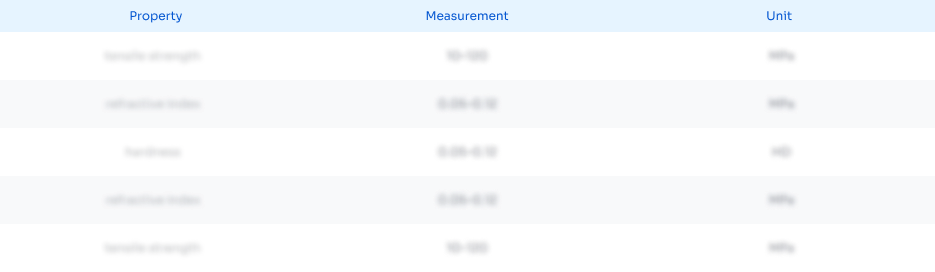
Abstract
Description
Claims
Application Information

- R&D
- Intellectual Property
- Life Sciences
- Materials
- Tech Scout
- Unparalleled Data Quality
- Higher Quality Content
- 60% Fewer Hallucinations
Browse by: Latest US Patents, China's latest patents, Technical Efficacy Thesaurus, Application Domain, Technology Topic, Popular Technical Reports.
© 2025 PatSnap. All rights reserved.Legal|Privacy policy|Modern Slavery Act Transparency Statement|Sitemap|About US| Contact US: help@patsnap.com