Floatation method of difficult-to-float coal
A coal slime flotation and difficult-to-float technology, applied in flotation, solid separation, etc., can solve the problems of low yield, hard-to-float slime cannot wash out qualified clean coal, etc., achieve large processing capacity per unit volume, improve drainage The effect of safety and buoyancy and process flexibility
- Summary
- Abstract
- Description
- Claims
- Application Information
AI Technical Summary
Problems solved by technology
Method used
Image
Examples
Embodiment 1
[0030] This embodiment adopts surface modification and two-stage microbubble direct flotation process. process such asfigure 1 shown.
[0031] Firstly, the coal slime water mixture with a particle size of less than 0.5mm (concentration is 120g / l), together with the collector kerosene, enters the surface modification machine from the coal slurry inlet of the cylindrical main barrel (produced by Changsha Kaitong Technology Co., Ltd., with a processing capacity of 1000m 3 / h, feed pressure 0.1MPa), the amount of kerosene added is 0.95g / l coal slime mixture, the speed of the surface modifier is 157rpm, the coal particles and collector in the coal slime water are carried out step by step through the curved turbine type stirring impeller Dispersion, mixing, scrubbing, shearing and stirring, under the action of the high-speed shear force field of the surface reformer, process for 90 seconds. After the coal surface modification is completed, it is discharged from the coal slurry outle...
Embodiment 2
[0035] The basic process is the same as that of Example 1, except that this example adopts a process flow of surface modification and a stage of microbubble direct flotation.
[0036] Add 0.8kg of collector light diesel oil and 0.16kg of GF flotation agent into every ton of difficult-to-float slime-water mixture (concentration: 140g / l).
[0037] The feeding pressure of the surface modifier is 0.2MPa, the rotation speed is 200rpm, and the treatment is 60 seconds.
[0038] The air pressure of the microbubble flotation machine is controlled at 0.1MPa.
Embodiment 3
[0040] The basic process is the same as in Example 1, except that 1.0 kg of collector kerosene and 0.1 kg of pine oil are added in every ton of difficult-to-float slime-water mixture (concentration is 140 g / l).
[0041] The feeding pressure of the surface modifier is 0.3MPa, the rotation speed is 100rpm, and the treatment is 80 seconds.
[0042] The air pressure of the microbubble flotation machine is controlled at 0.4MPa.
PUM
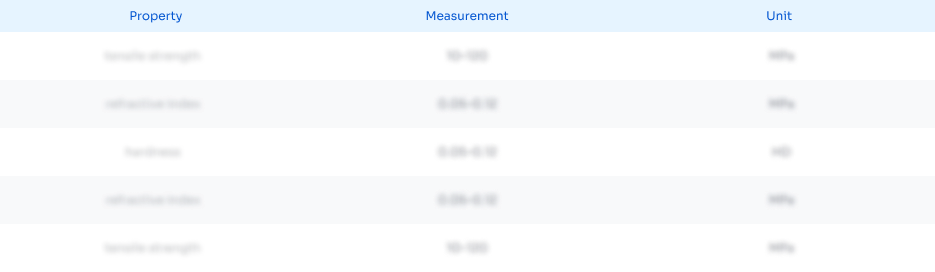
Abstract
Description
Claims
Application Information

- R&D
- Intellectual Property
- Life Sciences
- Materials
- Tech Scout
- Unparalleled Data Quality
- Higher Quality Content
- 60% Fewer Hallucinations
Browse by: Latest US Patents, China's latest patents, Technical Efficacy Thesaurus, Application Domain, Technology Topic, Popular Technical Reports.
© 2025 PatSnap. All rights reserved.Legal|Privacy policy|Modern Slavery Act Transparency Statement|Sitemap|About US| Contact US: help@patsnap.com