Method used for extracting iron from red mud by drastic reduction and method used for preparing gel material from secondary tailings
A cementitious material and deep technology, applied in the field of comprehensive utilization of resources, can solve the problems of low-grade iron-containing red mud being economically unreasonable, increasing production costs, and high smelting temperature, so as to solve the problem of red mud stockpiling, easy control and process. simple method effect
- Summary
- Abstract
- Description
- Claims
- Application Information
AI Technical Summary
Problems solved by technology
Method used
Image
Examples
Embodiment 1
[0015] (1) Deep reduction and iron extraction. Red mud contains 37.10% iron and contains Al 2 o 3 17.10%, containing SiO 2 7.46%, including CaO1.69%. Deep reduction conditions: red mud: coke: CaO=100:11:5, mixed evenly and kept at a reduction temperature of 1250°C for 60 minutes, then taken out and cooled naturally; Grinding at a grinding concentration of 65% to a fineness of -0.074 mm greater than 90%, the magnetic field strength is 111.44kA m -1 Under the conditions of magnetic separation, reduced iron powder with an iron grade of 91.23% and an iron recovery rate of 93.13% was obtained. Among them, the fixed carbon content of coke is 85.43%, the ash content is 12.5%, the volatile content is 1.21%, and the moisture content is 11.68%.
[0016] (2) Preparation of cementitious material from secondary tailings: filter and dry the secondary tailings after wet grinding and weak magnetic separation in step (1) and mix with blast furnace slag, cement clinker, activator and early...
Embodiment 2
[0018] (1) Deep reduction and iron extraction. Red mud contains 39.04% iron and contains Al 2 o 3 13.16%, containing SiO 2 8.02%, containing CaO1.55%. Deep reduction conditions: red mud: bituminous coal: CaO=100:17.5:12.5, mixed evenly and kept at a reduction temperature of 1350°C for 50 minutes, then taken out and cooled naturally; Grinding at a grinding concentration of 65% to a fineness of -0.074 mm greater than 90%, the magnetic field strength is 111.44kA m -1 Under the condition of magnetic separation, the reduced iron powder with iron grade of 92.58% and iron recovery rate of 95.05% was obtained. Among them, the fixed carbon content of bituminous coal is 67.83%, the ash content is 12.02%, the volatile content is 18.45%, and the moisture content is 1.48%.
[0019] (2) Preparation of cementitious material from secondary tailings: filter and dry the secondary tailings after wet grinding and weak magnetic separation in step (1) and mix with blast furnace slag, cement cl...
Embodiment 3
[0021] (1) Deep reduction and iron extraction. Red mud contains 37.10% iron and contains Al 2 o 3 17.10%, containing SiO 2 7.46%, including CaO1.69%. Deep reduction conditions: red mud: coke: CaF 2 : Na 2 CO 3 =100:11:5:10, after mixing evenly, keep it warm for 60min at the reduction temperature of 1250°C, then take it out and cool it naturally; grind the ore at a grinding concentration of 65% until the fineness -0.074mm is greater than 90%, and the magnetic field strength is 111.44kA·m -1 Under the conditions of magnetic separation, the reduced iron powder with an iron grade of 93.01% and an iron recovery rate of 92.84% was obtained. Among them, the fixed carbon content of coke is 85.43%, the ash content is 12.5%, the volatile content is 1.21%, and the moisture content is 11.68%.
[0022] (2) Preparation of cementitious material from secondary tailings: filter and dry the secondary tailings after wet grinding and weak magnetic separation in step (1) and mix with blast...
PUM
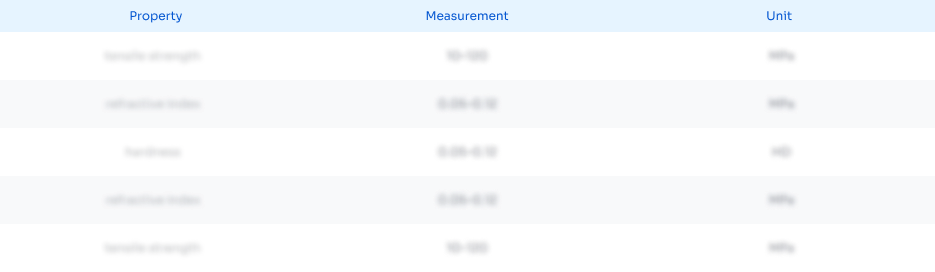
Abstract
Description
Claims
Application Information

- R&D
- Intellectual Property
- Life Sciences
- Materials
- Tech Scout
- Unparalleled Data Quality
- Higher Quality Content
- 60% Fewer Hallucinations
Browse by: Latest US Patents, China's latest patents, Technical Efficacy Thesaurus, Application Domain, Technology Topic, Popular Technical Reports.
© 2025 PatSnap. All rights reserved.Legal|Privacy policy|Modern Slavery Act Transparency Statement|Sitemap|About US| Contact US: help@patsnap.com