Manufacturing method of LGP (light guide plate)
A manufacturing method and technology of light guide plate, applied in the directions of light guide, optics, optical components, etc., can solve the problems of high cost and high equipment investment, and achieve the effect of reducing product cost, reducing investment cost and improving production yield
- Summary
- Abstract
- Description
- Claims
- Application Information
AI Technical Summary
Problems solved by technology
Method used
Image
Examples
Embodiment Construction
[0015] combine figure 1 , figure 2 , a method for manufacturing a light guide plate of the present invention is mainly used in the manufacture of a light guide plate for a backlight module or a flat light source, comprising the following steps:
[0016] Step 1: Prepare the light reflective material 1, the light reflective material 1 has a certain viscosity, and the light reflective material 1 can be prepared with high reflectivity materials such as silicon oxide, magnesium oxide, and titanium oxide;
[0017] Step 2: Print or coat the prepared light reflective material 1 on the reflective film or reflective paper 2 according to a certain shape and distribution method to make a uniform light reflective film;
[0018] Step 3: Dry the homogeneous reflective film, and then attach the release film (not shown in the release film diagram);
[0019] Step 4: Cut the dried homogeneous reflective film according to the size of the acrylic plate or other light-transmitting plate 2;
[0...
PUM
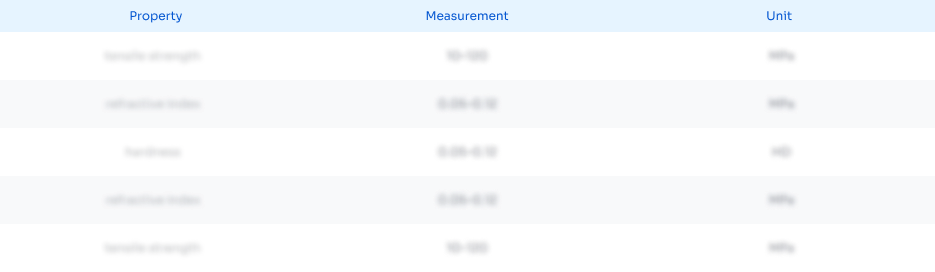
Abstract
Description
Claims
Application Information

- R&D
- Intellectual Property
- Life Sciences
- Materials
- Tech Scout
- Unparalleled Data Quality
- Higher Quality Content
- 60% Fewer Hallucinations
Browse by: Latest US Patents, China's latest patents, Technical Efficacy Thesaurus, Application Domain, Technology Topic, Popular Technical Reports.
© 2025 PatSnap. All rights reserved.Legal|Privacy policy|Modern Slavery Act Transparency Statement|Sitemap|About US| Contact US: help@patsnap.com