Method for producing aerated concrete with refuse incinerator slag
A technology of waste incineration slag and aerated concrete, which is applied in the field of solid waste resource utilization, can solve the problems of undiscovered research reports on waste incineration slag aerated concrete, and achieve the effect of reducing treatment costs and production costs
- Summary
- Abstract
- Description
- Claims
- Application Information
AI Technical Summary
Problems solved by technology
Method used
Examples
Embodiment 1
[0042] Example 1 The method of producing air-entrained concrete with waste incineration slag: the air-entrained concrete composition contains 57% fly ash, 20% quicklime, 10% P.0.42.5 ordinary Portland cement, 3% gypsum, 10% Garbage incineration slag.
[0043] The total water-to-material ratio is 0.60-0.70, and the mixing water is warm water at 60°C. Add fly ash and water to make a slurry, stir for 3-4 minutes, add cement, stir for 3-4 minutes, add gypsum, stir for 2-3 minutes, add quicklime, stir for 2-3 minutes, pump until the slurry is poured and stirred In the tank, turn on the pouring car owner's mixer for secondary mixing. Add the measured garbage incinerator slag, stir for 30-50s, inject into the mold to generate gas, stop at 60°C for 2 hours, and cut into pieces. Send it into the autoclave, autoclave at 170-180°C and 0.8-1.2MPa pressure, and leave the autoclave at constant temperature for 8-10 hours.
[0044] The product leaves the factory after 4-7 days of natural c...
Embodiment 2
[0045] Example 2 The method of producing air-entrained concrete with waste incineration slag: the air-entrained concrete composition contains 57% granulated blast furnace slag, 20% quicklime, 10% P.0.42.5 ordinary Portland cement, 3% gypsum, 10 % Garbage incineration slag.
[0046] The total water-to-material ratio is 0.60-0.70, and the mixing water is warm water at 60°C. Add water to granulated blast furnace slag to make a slurry, stir for 3-4 minutes, add cement, stir for 3-4 minutes, add gypsum, stir for 2-3 minutes, add quicklime, stir for 2-3 minutes, pump until pouring car slurry In the mixing tank, turn on the pouring car owner's mixer for secondary mixing. Add the measured garbage incinerator slag, stir for 30-50s, inject into the mold to generate gas, stop at 60°C for 2 hours, and cut into pieces. Send it into the autoclave, autoclave at 180-190°C and 1.0-1.2MPa pressure, and leave the autoclave at constant temperature for 6-8 hours.
[0047] The product leaves the...
Embodiment 3
[0048] Example 3 The method of producing air-entrained concrete with waste incineration slag: the air-entrained concrete composition contains 38-42% quartz sand, 30-32% slag, 18-20% P.0.42.5 ordinary Portland cement, 10 % Garbage incineration slag, and an appropriate amount of gas-generating regulator.
[0049] The total water-to-material ratio is 0.30-0.50, and the mixing water is warm water at 60°C. Mix the slag, quartz sand and cement dry powder evenly, beat the slurry and mix evenly, stir for 3-4 minutes, pump it into the slurry mixing tank of the pouring car, turn on the main mixer of the pouring car, and perform the second mixing. Add the measured garbage incinerator slag, stir for 15-30s, inject into the mold to generate gas, stop at 60°C for 2 hours, and cut into pieces. Send it into the autoclave, autoclave at 210°C and 1.5MPa pressure, and leave the autoclave at constant temperature for 6-8 hours.
[0050] The product leaves the factory after 4-7 days of natural cu...
PUM
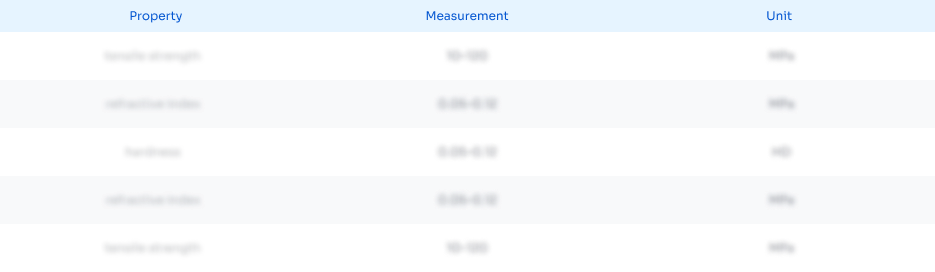
Abstract
Description
Claims
Application Information

- Generate Ideas
- Intellectual Property
- Life Sciences
- Materials
- Tech Scout
- Unparalleled Data Quality
- Higher Quality Content
- 60% Fewer Hallucinations
Browse by: Latest US Patents, China's latest patents, Technical Efficacy Thesaurus, Application Domain, Technology Topic, Popular Technical Reports.
© 2025 PatSnap. All rights reserved.Legal|Privacy policy|Modern Slavery Act Transparency Statement|Sitemap|About US| Contact US: help@patsnap.com