Metal surface treatment method
A technology for metal surface treatment and metal workpieces, applied in anodizing and other directions, can solve the problems of wear resistance, scratch resistance, can not achieve ceramic performance and effect, does not have ceramic enamel texture, etc., to achieve the effect of good surface appearance and performance
- Summary
- Abstract
- Description
- Claims
- Application Information
AI Technical Summary
Problems solved by technology
Method used
Examples
Embodiment 1
[0030] The aluminum metal workpiece is degreased and dewaxed in alloy degreasing powder 50g / L for 4 minutes, and then alkali-etched in a NaOH solution with a concentration of 60g / L and a temperature of 70±10°C for 15s, and then placed in Neutralize in a 40% nitric acid solution to fully clean the surface.
[0031] Then the workpiece is placed in the anodic oxidation solution for anodic oxidation treatment; the concentration of sulfuric acid in the anodic oxidation solution is 180g / L, the concentration of aluminum ions is 6g / L, the temperature of the anodic oxidation solution is 19-20°C, and the DC voltage is set as 15V, the oxidation time is 40 minutes.
[0032] Then use inkjet printing to print patterns on the surface of the workpiece. The inkjet printing machine used is the model AT6001 digital printing machine produced by Shenzhen Yueda Color Printing. The ink used is dye solvent ink, and the main component of dye is Ingredients Phthalocyanine dyes. Let the workpiece stan...
Embodiment 2
[0035] The aluminum alloy workpiece is degreased and dewaxed in alloy degreasing powder 50g / L for 4 minutes, and then subjected to alkali etching treatment in NaOH solution with a concentration of 60g / L and a temperature of 70±10°C for 15s.
[0036] Then place the workpiece in a chemical whitening solution for 50 seconds. The whitening solution contains 1.5 mol / L of ammonium bifluoride and 0.45 mol / L of ammonium sulfate; the temperature of the solution is controlled at 25°C. Then place it in a nitric acid solution with a concentration of 40% for neutralization treatment, and fully clean the surface for 10 seconds.
[0037]Then the workpiece is placed in the anodic oxidation solution for anodic oxidation treatment; the concentration of sulfuric acid in the anodic oxidation solution is 180g / L, the concentration of aluminum ions is 6g / L, the temperature of the anodic oxidation solution is 19-20°C, and the DC voltage is set as 15V, the oxidation time is 40 minutes.
[0038] Then ...
Embodiment 3
[0041] The aluminum alloy workpiece is degreased and dewaxed in alloy degreasing powder 50g / L for 4 minutes, and then subjected to alkali etching treatment in NaOH solution with a concentration of 60g / L and a temperature of 70±10°C for 15s.
[0042] Then place the workpiece in a chemical whitening solution for 80 seconds. The whitening solution includes 1 mol / L of ammonium bifluoride and 0.4 mol / L of ammonium sulfate; the temperature of the solution is controlled at 30°C. Then place it in a nitric acid solution with a concentration of 40% for neutralization treatment, and fully clean the surface for 15 seconds.
[0043] Then the workpiece is placed in an anodic oxidation solution for anodic oxidation treatment, the concentration of sulfuric acid in the anodic oxidation solution is 160g / L, the concentration of aluminum ions is 8g / L, the temperature of the anodic oxidation solution is 19-20°C, and the DC voltage is set to 13V, the oxidation time is 35 minutes.
[0044] Then use...
PUM
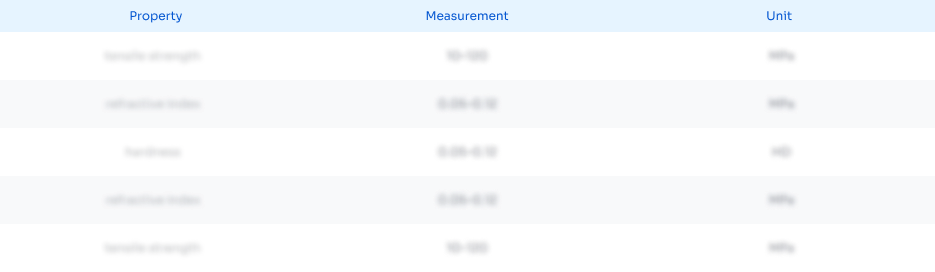
Abstract
Description
Claims
Application Information

- Generate Ideas
- Intellectual Property
- Life Sciences
- Materials
- Tech Scout
- Unparalleled Data Quality
- Higher Quality Content
- 60% Fewer Hallucinations
Browse by: Latest US Patents, China's latest patents, Technical Efficacy Thesaurus, Application Domain, Technology Topic, Popular Technical Reports.
© 2025 PatSnap. All rights reserved.Legal|Privacy policy|Modern Slavery Act Transparency Statement|Sitemap|About US| Contact US: help@patsnap.com