Sosoloid toughened metal ceramic and preparation method thereof
A cermet and solid solution technology, which is applied in the field of solid solution toughened cermet and its preparation, can solve the problem of low fracture toughness and achieve the effects of good thermal shock resistance, short time and low energy consumption
- Summary
- Abstract
- Description
- Claims
- Application Information
AI Technical Summary
Problems solved by technology
Method used
Image
Examples
Embodiment 1
[0021] Embodiment 1, including pre-solution treatment step, raw material mixing step, molding step, degreasing step and vacuum sintering step:
[0022] 1. Pre-solution treatment step: according to the mass percentage shown in Table 1, TiO 2 Powder, W powder and C powder are divided into three groups with equal amounts of A1, A2 and A3, wherein, the average particle size, purity and oxygen content of each raw material powder are shown in Table 2; after each group is mixed, A1 group, A2 group, Group A3 is further divided into three groups, a total of nine groups of raw material powder, using ball mill dry ball milling, to obtain nine groups of ball abrasives B1 ~ B9, of which three groups of ball abrasives B1, B2, B3 correspond to the raw material powder of group A1, B4, B5, The three groups of ball abrasives of B6 correspond to the raw material powder of group A2, the three groups of ball abrasives of B7, B8 and B9 correspond to the raw material powder of group A3, and the spec...
Embodiment 2
[0047] 1. Pre-solution treatment step: TiO 2 Powder, W powder and graphite powder are batched according to the mass percentage shown in A3 in Table 2, and then ball milled according to the process shown in B9 in Table 3. Put the ball abrasive into the graphite burning boat, carry out carbothermal reduction treatment according to the P9 process in Table 4 in the vacuum furnace, and obtain the nominal composition of (Ti 0.62 , W 0.38 ) the pre-solid solution powder of C;
[0048] 2. Raw material mixing step: according to the mass percentage shown in Table 9, the (Ti 0.62 , W 0.38 ) C solid solution powder was mixed with TiC powder, Mo powder, graphite powder and Ni powder respectively, and then wet milled on a ball mill with a ball-to-material ratio of 6:1, a rotational speed of 150 rpm, and a time of 36 hours to obtain F0, F1, F2, and F3 , F4, F5 and F6 a total of seven groups of mixed slurry, wherein, F0 does not contain (Ti 0.62 , W 0.38 ) C solid solution powder formul...
Embodiment 3
[0060] 1. Pre-solution treatment step: according to the mass percentage of A2 in Table 2, TiO 2 Powder, W powder and graphite powder were mixed, and ball milled according to the B5 process in Table 3. Then put the ball abrasive into the graphite burning boat, carry out carbothermal reduction treatment in the vacuum carbon tube furnace, the temperature is 1370 ℃, keep the temperature for 2h, and the nominal composition is (Ti 0.77 , W 0.23 ) the pre-solid solution powder of C;
[0061] 2. Raw material mixing step: according to the mass percentage shown in Table 12, the (Ti 0.77 , W 0.23 ) C solid solution powder was mixed with TiC powder, Mo powder, graphite powder and Ni powder respectively, and wet milled on a ball mill with a ball-to-material ratio of 5:1, a rotating speed of 200rpm, and a time of 24h to obtain I1, I2, I3, I4, I5, I6, I7, I8 and I9 have a total of nine groups of mixed slurry, put the mixed slurry in a drying oven for drying, the drying temperature is 85 ...
PUM
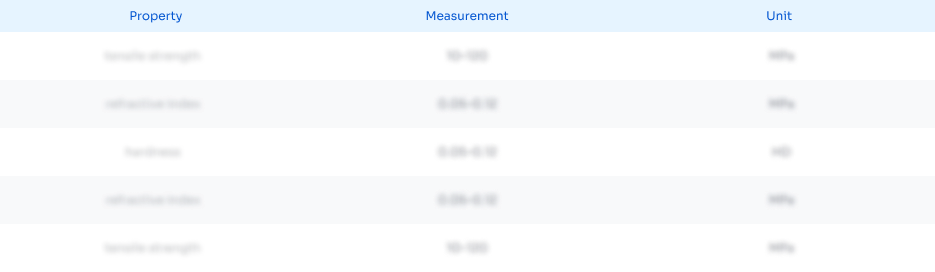
Abstract
Description
Claims
Application Information

- R&D
- Intellectual Property
- Life Sciences
- Materials
- Tech Scout
- Unparalleled Data Quality
- Higher Quality Content
- 60% Fewer Hallucinations
Browse by: Latest US Patents, China's latest patents, Technical Efficacy Thesaurus, Application Domain, Technology Topic, Popular Technical Reports.
© 2025 PatSnap. All rights reserved.Legal|Privacy policy|Modern Slavery Act Transparency Statement|Sitemap|About US| Contact US: help@patsnap.com