Hydrous silane coupling agent-polyether grafted polysiloxane polymer coating
A technology of silane coupling agent and polysiloxane, which is applied in the field of coatings, can solve the problems of poor hardness, poor compatibility of inorganic interior and exterior wall coatings, easy cracking and falling off, etc., and achieve stable film formation, excellent film appearance and fixation effect Good results
- Summary
- Abstract
- Description
- Claims
- Application Information
AI Technical Summary
Problems solved by technology
Method used
Image
Examples
Embodiment 1
[0036] Embodiment 1: Preparation of aqueous silane coupling agent-polyether graft polysiloxane polymer coating
[0037] Add 100g of hydrogen-containing silicone oil (M n =2000g / mol), 80g polyether (M n =800g / mol) and 200g toluene, under stirring, blow nitrogen at 50°C for 30min, add 0.05gH 2 PtCl 6 , under the protection of nitrogen, the temperature was raised to 110°C for 5 hours to obtain a polyether-grafted polymethylsiloxane solution; 20 g of 3-(acryloyloxy)propoxypropyltrimethoxysilane was added dropwise within 1 hour, and continued After reacting for 6 hours, the aqueous silane coupling agent-polyether grafted polysiloxane polymer was obtained.
[0038] Get the potassium silicate aqueous solution 100g that modulus is 2.9, the aqueous silane coupling agent-polyether graft polysiloxane polymer 5g of above-mentioned preparation, water 50g, titanium dioxide 20g, ferric oxide 10g, calcium carbonate 30g, Silicon dioxide 20g, mineral oil defoamer (TEGO Foamex K3) 0.08g, acr...
Embodiment 2
[0039] Embodiment 2: Preparation of aqueous silane coupling agent-polyether graft polysiloxane polymer coating
[0040] Add 100g of hydrogen-containing silicone oil (M n =1000g / mol), 120g polyether (M n =500g / mol) and 350g of toluene, under stirring, purging with nitrogen for 30min at 80°C, adding 0.1gK 2 PtCl 4 , under the protection of nitrogen, the temperature was raised to 100°C for 8 hours to obtain a polyether-grafted polymethylsiloxane solution; 50 g of 3-(acryloyloxy)propoxypropyltrimethoxysilane was added dropwise within 2 hours, and continued After reacting for 8 hours, an aqueous silane coupling agent-polyether grafted polysiloxane polymer was obtained.
[0041] Take 100 g of sodium silicate aqueous solution with a modulus of 2.0, 50 g of the aqueous silane coupling agent-polyether graft polysiloxane polymer prepared above, 10 g of water, 40 g of titanium dioxide, 20 g of calcium carbonate, polysiloxane disinfectant Foaming agent (BYK066) 1g, acrylic acid sodium...
Embodiment 3
[0042] Embodiment 3: Preparation of aqueous silane coupling agent-polyether graft polysiloxane polymer coating
[0043] Add 100g of hydrogen-containing silicone oil (M n =5000g / mol), 100g polyether (M n =1500g / mol) and 200g cyclohexanone, under stirring, nitrogen purging at 90°C for 30min, adding 0.5gPt(CH 2 =CHPh) 2 Cl 2 , under the protection of nitrogen, the temperature was raised to 150°C for 3 hours to obtain a polyether-grafted polymethylsiloxane solution; 10 g of 3-(acryloyloxy)propoxypropyltrimethoxysilane was added dropwise within 0.5 hours, The reaction was continued for 3 hours to obtain a water-based silane coupling agent-polyether grafted polysiloxane polymer.
[0044] Take modulus 3.0 sodium silicate aqueous solution 20g, modulus 2.6 potassium silicate aqueous solution 80g, aqueous silane coupling agent-polyether grafted polysiloxane polymer 20g, water 100g, titanium dioxide 15g, oxidation 40g copper, 50g calcium carbonate, 10g silicon dioxide, 2g mineral oi...
PUM
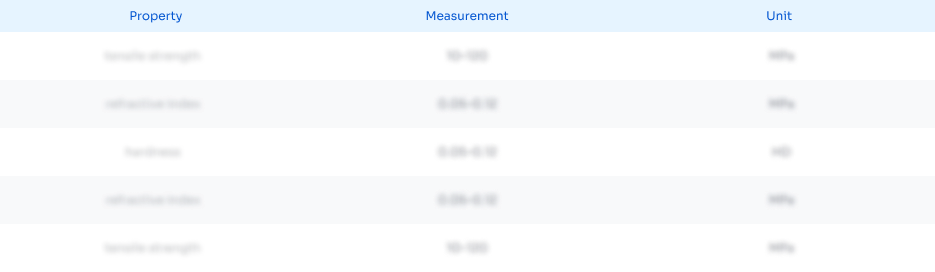
Abstract
Description
Claims
Application Information

- R&D Engineer
- R&D Manager
- IP Professional
- Industry Leading Data Capabilities
- Powerful AI technology
- Patent DNA Extraction
Browse by: Latest US Patents, China's latest patents, Technical Efficacy Thesaurus, Application Domain, Technology Topic, Popular Technical Reports.
© 2024 PatSnap. All rights reserved.Legal|Privacy policy|Modern Slavery Act Transparency Statement|Sitemap|About US| Contact US: help@patsnap.com