Plaster mould for ceramic slip casting and manufacturing method of plaster mould
A gypsum mold and grouting molding technology, applied in the field of gypsum mold and its preparation, can solve the problems of poor water absorption performance and low strength, and achieve the effects of improving corrosion resistance and wear resistance, high strength and strong corrosion resistance
- Summary
- Abstract
- Description
- Claims
- Application Information
AI Technical Summary
Problems solved by technology
Method used
Examples
preparation example Construction
[0018] The present invention also provides a kind of preparation method of gypsum mold, and this method comprises the following steps:
[0019] S1 uses asphalt as raw material, adds foaming agent and mixes evenly, and foams under the protection of nitrogen atmosphere to prepare porous pitch carbon;
[0020] S2 Prepare gypsum powder and water to make gypsum slurry, mix gypsum slurry with pitch charcoal, stir, cast, and dry to make a gypsum mold.
[0021] According to the preparation method of the gypsum mold provided by the present invention, preferably, the foaming temperature is 350-600°C, the pressure is 2-5MPa, the heating rate is 5-15°C / min, and the temperature is kept at the highest temperature for 2-5h .
[0022] According to the method for preparing a gypsum mold provided by the present invention, preferably, the foaming agent is an inorganic foaming agent and / or an organic foaming agent. More preferably, described inorganic foaming agent is at least one in sodium bic...
Embodiment 1
[0030] 1. Preparation of porous pitch carbon: high-temperature coal tar pitch (softening point 95°C) is used as raw material, ammonium carbonate is used as foaming agent, and the two are mixed evenly at a mass ratio of 100:1. The obtained mixture was foamed in an autoclave to prepare porous pitch carbon. The foaming process was as follows: heating rate 10°C / min, pressure 3MPa, maximum foaming temperature 500°C and heat preservation for 4h. The obtained bituminous charcoal is broken into particles with a particle size of 3-8 mm.
[0031] 2. Preparation of gypsum slurry: gypsum powder with a purity of more than 95% and a particle size of 90-150 mesh (wherein α gypsum powder: β gypsum powder = 80:20) is mixed with water and stirred under the condition of a vacuum of 0.0008MPa. Gypsum slurry, wherein the mass ratio of gypsum powder to water is 1.2:1.
[0032] 3. Preparation of gypsum mold: Take the porous pitch carbon and gypsum slurry prepared by the above method, and mix 35 p...
Embodiment 2
[0035] The gypsum mold was prepared by the same method as in Example 1, except that the foaming agent was replaced with aliphatic amine (1.5wt% added); the foaming process was: heating rate 15°C / min, pressure 2MPa, the highest foaming The temperature is 600° C. and the temperature is kept for 2 hours; in the gypsum slurry, the mass ratio of gypsum powder to water is 1:1; the gypsum mold A2 is prepared.
PUM
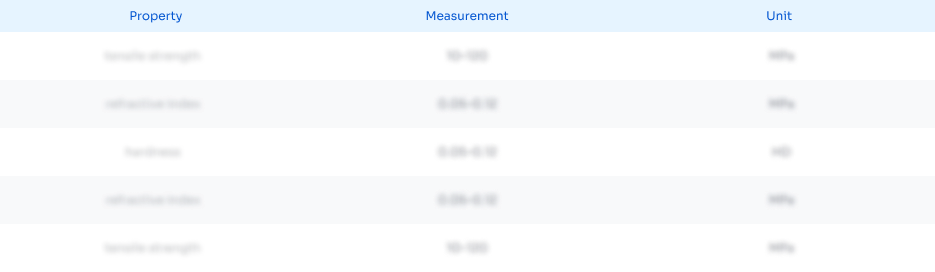
Abstract
Description
Claims
Application Information

- R&D
- Intellectual Property
- Life Sciences
- Materials
- Tech Scout
- Unparalleled Data Quality
- Higher Quality Content
- 60% Fewer Hallucinations
Browse by: Latest US Patents, China's latest patents, Technical Efficacy Thesaurus, Application Domain, Technology Topic, Popular Technical Reports.
© 2025 PatSnap. All rights reserved.Legal|Privacy policy|Modern Slavery Act Transparency Statement|Sitemap|About US| Contact US: help@patsnap.com