Magnesium hydride (MgH2) and ferrum-containing sulfide composite hydrogen storage material and preparation method thereof
A composite material and sulfide technology, applied in the field of hydrogen storage materials, can solve the problems of insignificant improvement in dehydrogenation temperature, high price, and restrictions, and achieve the effects of easy industrialization and promotion, low cost, and low energy consumption
- Summary
- Abstract
- Description
- Claims
- Application Information
AI Technical Summary
Problems solved by technology
Method used
Image
Examples
Embodiment 1
[0023] In an argon-protected glove box, the MgH 2 Powder and Fe 3 S 4 The powder is mixed in a ball mill at a mass ratio of 4:1. The balls are stainless steel. The ball mill is a Pulverisette 6 planetary ball mill. The speed of the ball mill is 450r / min. The time was 2h, then filled with high-purity argon gas of 0.1MPa, and adopted high-energy ball milling. MgH prepared by ball milling 2 The composite hydrogen storage material was tested for hydrogen absorption rate, and the results were as follows figure 1 shown. From the hydrogen absorption rate curve at 423K in the figure, it can be seen that the MgH 2 add Fe 3 S 4 The composite hydrogen storage material prepared after ball milling can reach 80% of the maximum hydrogen absorption in 30s, and in about 25min, the hydrogen absorption is 3.5 times that of the alloy without additives, but without Fe. 3 S 4 MgH 2 It takes 900s for the sample to reach 80% of the maximum hydrogen absorption capacity. It can be seen that ...
Embodiment 2
[0025] In an argon-protected glove box, the MgH 2 Powder and Fe 3 S 4 The powder is mixed in a ball mill at a mass ratio of 9:1. The balls are stainless steel. The ball mill is a Pulverisette 6 planetary ball mill. The speed of the ball mill is 550r / min. The time was 3h, then filled with high-purity argon gas of 0.5MPa, and adopted high-energy ball milling. MgH prepared by ball milling 2 The composite hydrogen storage material was tested for hydrogen absorption rate, and the results were as follows figure 2 shown. From the hydrogen absorption rate curve at 473K in the figure, it can be seen that the MgH 2 add Fe 3 S 4 The composite hydrogen storage material prepared after ball milling can reach 80% of the maximum hydrogen absorption capacity within 30 s without adding Fe. 3 S 4 MgH 2 It takes 900s for the sample to reach 80% of the maximum hydrogen absorption capacity. It can be seen that the iron-containing sulfide and MgH provided by the present invention 2 The ...
Embodiment 3
[0027] In an argon-protected glove box, the MgH 2 Powder and Fe 3 S 4 The powder is mixed in a ball mill at a mass ratio of 7:3. The balls are stainless steel. The ball mill is a Pulverisette 6 planetary ball mill. The speed of the ball mill is 550r / min. The time was 3h, then filled with high-purity argon gas of 0.1MPa, adopted high-energy ball milling method, cooled to room temperature naturally after the ball milling, and packaged in a glove box protected by argon gas. MgH prepared by ball milling 2 The hydrogen desorption rate test was carried out on the composite hydrogen storage material, and the results were as follows image 3shown. From the hydrogen evolution rate curve at 573K in the figure, it can be seen that the direction of MgH 2 add Fe 3 S 4 The composite hydrogen storage material prepared after ball milling can reach 80% of the maximum hydrogen release in 200s without adding Fe. 3 S 4 MgH 2 It takes 1000s to reach 80% of the maximum hydrogen release. ...
PUM
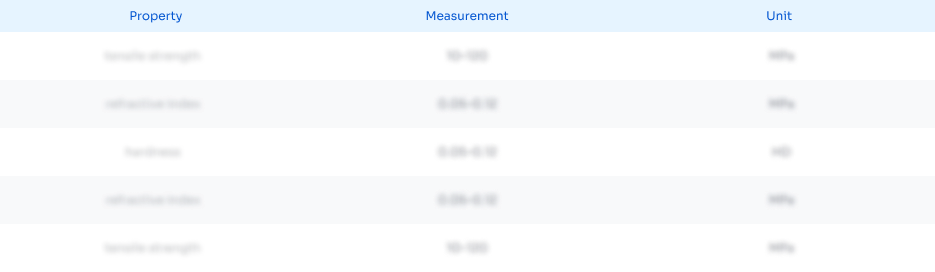
Abstract
Description
Claims
Application Information

- R&D
- Intellectual Property
- Life Sciences
- Materials
- Tech Scout
- Unparalleled Data Quality
- Higher Quality Content
- 60% Fewer Hallucinations
Browse by: Latest US Patents, China's latest patents, Technical Efficacy Thesaurus, Application Domain, Technology Topic, Popular Technical Reports.
© 2025 PatSnap. All rights reserved.Legal|Privacy policy|Modern Slavery Act Transparency Statement|Sitemap|About US| Contact US: help@patsnap.com