Thermoforming steel with tensile strength of 1,700MPa level and production method thereof
A 1700mpa, tensile strength technology, applied in the field of tensile strength 1700MPa hot-formed steel and its production, can solve the problems of low production efficiency, poor, high plasticity, etc., to achieve the effect of reducing body weight and protecting safety
- Summary
- Abstract
- Description
- Claims
- Application Information
AI Technical Summary
Problems solved by technology
Method used
Image
Examples
Embodiment Construction
[0050] A detailed description is given below:
[0051] Table 1 is the components and values of each embodiment of the present invention and comparative examples;
[0052] Table 2 is the value of the main process parameters of each embodiment of the present invention and comparative example;
[0053] Table 3 shows the detected values of mechanical properties corresponding to the various embodiments of the present invention and comparative examples.
[0054] The method for producing 1700MPa grade hot forming steel of tensile strength, its steps:
[0055] 1) Hot metal desulfurization and converter smelting, control the smelting end point C: 0.05~0.06%, P: ≤0.008%, S: ≤0.002%, N: ≤0.004%, O: ≤0.004%, and the tapping temperature is 1700~ 1780°C, slag thickness 60-80mm;
[0056] 2) Converter smelting and continuous casting into billets;
[0057] 3) Heat the billet to 1280-1320°C, and control the heating rate at 350-400°C / hour;
[0058] 4) Carry out rough rolling, and contro...
PUM
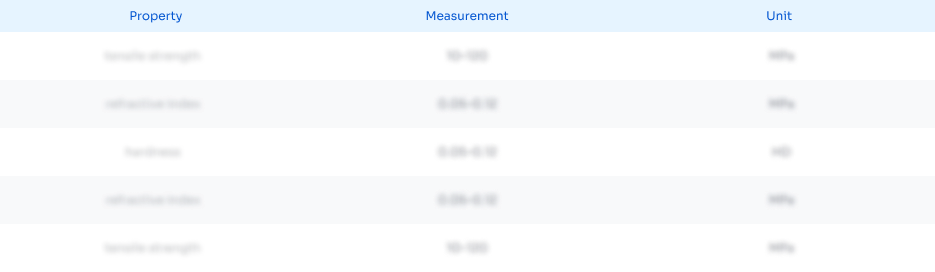
Abstract
Description
Claims
Application Information

- R&D
- Intellectual Property
- Life Sciences
- Materials
- Tech Scout
- Unparalleled Data Quality
- Higher Quality Content
- 60% Fewer Hallucinations
Browse by: Latest US Patents, China's latest patents, Technical Efficacy Thesaurus, Application Domain, Technology Topic, Popular Technical Reports.
© 2025 PatSnap. All rights reserved.Legal|Privacy policy|Modern Slavery Act Transparency Statement|Sitemap|About US| Contact US: help@patsnap.com