Direct torque control method of brushless DC motor based on segmented sliding mode variable structure
A direct torque control, sliding mode variable structure technology, applied in the direction of a single motor speed/torque control, torque ripple control, etc., can solve the difficulty of extracting back EMF, without considering the adverse effects of the system, and the actual application effect is not ideal, etc. question
- Summary
- Abstract
- Description
- Claims
- Application Information
AI Technical Summary
Problems solved by technology
Method used
Image
Examples
Embodiment 1
[0053] figure 1 It is the block diagram of the direct torque control of the segmented sliding mode variable structure brushless DC motor proposed by the present invention. The segmented sliding mode variable structure state observer completes the reconstruction and extraction of the motor back EMF, and the space vector switch state selector completes the on-off control of the six switching tubes of the three-phase inverter power supply. In the three-phase six-state control mode, the rotating space of the flux linkage can be divided into six sections. According to the actual needs of the system, given the angular velocity and stator flux linkage, the torque tolerance and flux linkage tolerance are reasonably designed. Obtain the a and b two-phase currents through the current sensor and 2 A / D converters. The motor speed is obtained by the speed measuring device. The torque and flux linkage are estimated in real time according to the stator flux linkage and torque calculation formu...
PUM
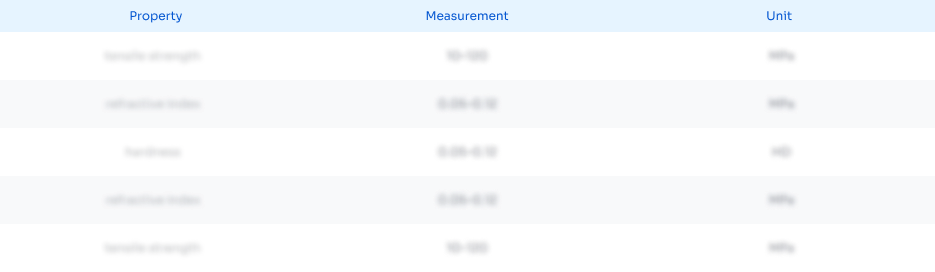
Abstract
Description
Claims
Application Information

- R&D Engineer
- R&D Manager
- IP Professional
- Industry Leading Data Capabilities
- Powerful AI technology
- Patent DNA Extraction
Browse by: Latest US Patents, China's latest patents, Technical Efficacy Thesaurus, Application Domain, Technology Topic, Popular Technical Reports.
© 2024 PatSnap. All rights reserved.Legal|Privacy policy|Modern Slavery Act Transparency Statement|Sitemap|About US| Contact US: help@patsnap.com