Process for synthesizing diacetylmonoxime ethyl ether by continuous reactions in microtube
A butanone oxime internal reaction technology, applied in the field of continuous microtube internal reaction synthesis of butanone oxime ether, can solve the problems of long operation time, low equipment utilization rate, excessive progress, etc., achieve mass transfer and heat transfer process enhancement, Effects of reduced operating time and cost and stable operation time
- Summary
- Abstract
- Description
- Claims
- Application Information
AI Technical Summary
Problems solved by technology
Method used
Image
Examples
Embodiment 1
[0028] The inner diameter of the microtube reactor is 2.1mm and the length is 5m.
[0029] Butanone oxime, diethyl sulfate, and 18% aqueous sodium hydroxide solution are in a material ratio of 1:1.25:1.15. Feed continuously, the reaction temperature is 30°C, and the residence time is 20min. The reaction product is collected by low-temperature condensation, and the oil phase is obtained after the product is separated and separated, and the residual organic matter in the water phase is extracted and recovered with an extractant. The product was analyzed by gas chromatography with GC1690 gas chromatograph. The chromatographic column is a GsBP-INOWAX (specification: 30m×0.32mm×0.25μm) type capillary column, FID detector, and n-butanol is used as the internal standard for quantitative calculation. Analysis method, the same below. The conversion rate of butanone oxime is 83.41%, the yield of butanone oxime ethyl ether is 16.80%, and the selectivity is 16.80%.
Embodiment 2
[0031] The inner diameter of the microtube reactor is 2.1mm and the length is 5m.
[0032] Butanone oxime, diethyl sulfate, and 18% aqueous sodium hydroxide solution are in a ratio of 1:1:1. Feed continuously, the reaction temperature is 30°C, and the residence time is 3min. The reaction product is collected by low-temperature condensation, the product is separated and separated to obtain the oil phase, and the residual organic matter in the water phase is extracted and recovered with an extractant, and the product is analyzed by gas chromatography. The conversion rate of butanone oxime is 87.64%, the yield of butanone oxime ethyl ether is 15.81%, and the selectivity is 18.04%.
Embodiment 3
[0034] The inner diameter of the microtube reactor is 1mm and the length is 20m.
[0035] Butanone oxime, diethyl sulfate, and 18% aqueous sodium hydroxide solution are in a ratio of 1:1:1. Feed continuously, the reaction temperature is 40°C, and the residence time is 60min. The reaction product is collected by low-temperature condensation, the product is separated and separated to obtain the oil phase, and the residual organic matter in the water phase is extracted and recovered with an extractant, and the product is analyzed by gas chromatography. The conversion rate of butanone oxime is 77.87%, the yield of butanone oxime ethyl ether is 53.10%, and the selectivity is 68.19%.
PUM
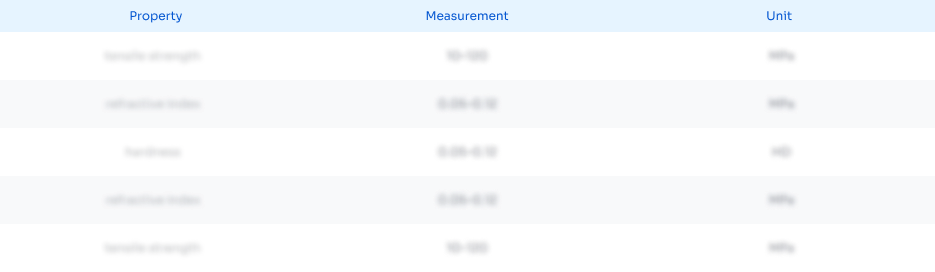
Abstract
Description
Claims
Application Information

- R&D
- Intellectual Property
- Life Sciences
- Materials
- Tech Scout
- Unparalleled Data Quality
- Higher Quality Content
- 60% Fewer Hallucinations
Browse by: Latest US Patents, China's latest patents, Technical Efficacy Thesaurus, Application Domain, Technology Topic, Popular Technical Reports.
© 2025 PatSnap. All rights reserved.Legal|Privacy policy|Modern Slavery Act Transparency Statement|Sitemap|About US| Contact US: help@patsnap.com