Integrated spinning method combined with compact spinning, siro spinning and sirofil spinning
A technology of sirofil spinning and integrated spinning, applied in the field of spinning in textile engineering, can solve the problems of low efficiency of concentrated spinning, unable to produce normally, filament color limitation, etc. High efficiency, good coating effect and high strength
- Summary
- Abstract
- Description
- Claims
- Application Information
AI Technical Summary
Problems solved by technology
Method used
Image
Examples
Embodiment 1
[0022] Example 1: Spinning low-cost and high-quality wool compact Siro core-spun yarn.
[0023] Two wool rovings a and a' are unwound from the roving ball, pass through the three-way yarn splitter 1 respectively, keep a distance of 8mm, and enter in parallel to the back roller 2, back roller 2', three-way bell mouth 3, The drafting area composed of middle top roller 4, apron 5, middle roller 4', lower apron 5', front top roller 6 and front roller 6'; the two strands formed by the roving after drafting, enter the double In the negative pressure accumulation area of the hole-row apron 8, the distance between the double rows of holes is 6 mm; the gathered two strands and the 30D viscose filament b transported by the positioning guide wheel 9 enter the holding roller 7 in parallel and 7', wherein the viscose filament b is in the middle of the two whiskers; after being held, the two whiskers and the viscose filament b converge and are twisted and wound into a yarn.
[0024] The ...
Embodiment 2
[0025] Example 2: Spinning high-count and high-ratio wool-polyester accumulated Siro core-spun yarn.
[0026] Select the 0.19 g / m roving a and a' of 0.19 g / m blended with 110 ultra-fine wool and 1.5D ultra-fine polyester in a 50 / 50 ratio, and unwind from the roving ball, respectively. Pass through the three-way yarn splitter 1 in parallel and enter the drafting area, and the two strands formed after the roving is drafted 24.5 times enter the negative pressure accumulation area of the double-row hole apron 8 in parallel, and the distance between the double-row holes is 6mm; The gathered two strands and the polyester filament b with a fineness of 20D conveyed by the positioning guide wheel 9 enter the holding rollers 7 and 7' in parallel, wherein the polyester filament b is in the middle of the two strands; After being held, the two strands and the filament b are converged, twisted, wound into yarn, and spun into a 6.67×3 tex (150Nm / 3) compacted Siro core-spun yarn.
[0027] ...
Embodiment 3
[0028] Example 3: Coating functional filaments to endow yarns with different functions.
[0029] Two light yellow wool rovings a and a' are unwound from the roving ball, respectively pass through the three-way yarn splitter 1 in parallel, and enter the drafting area. The two strands formed by the roving after drafting enter the double row In the negative pressure accumulation area of the hole apron 8, the distance between the double rows of holes is 7 mm; the two gathered strands enter the holding rollers 7 and 7 in parallel with the silver-plated filament b conveyed by the positioning guide wheel 9 ’, wherein the silver-plated filament b is in the middle of the two strands; after being held, the two strands and the filament b converge and are twisted and wound into a yarn.
[0030] Because the silver-plated filament will change color after being treated at a certain temperature, the use of ordinary Siro spinning and Sirofill varieties is limited. Due to the lax coating, the...
PUM
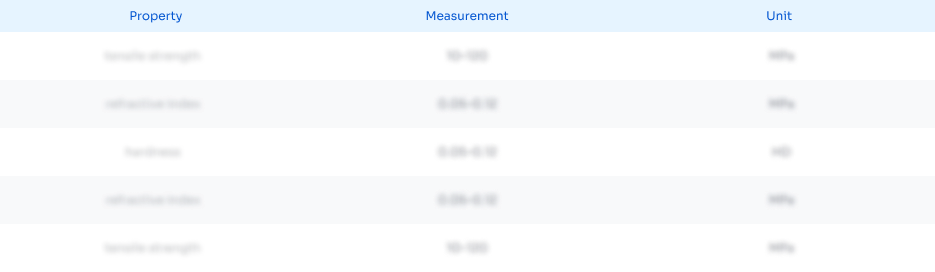
Abstract
Description
Claims
Application Information

- R&D
- Intellectual Property
- Life Sciences
- Materials
- Tech Scout
- Unparalleled Data Quality
- Higher Quality Content
- 60% Fewer Hallucinations
Browse by: Latest US Patents, China's latest patents, Technical Efficacy Thesaurus, Application Domain, Technology Topic, Popular Technical Reports.
© 2025 PatSnap. All rights reserved.Legal|Privacy policy|Modern Slavery Act Transparency Statement|Sitemap|About US| Contact US: help@patsnap.com