Improved screen print production line of figure-number steel plates
A technology of screen printing and production line, applied in screen printing machine, printing, printing machine and other directions, can solve the problems of inability to transfer steel belt roll coating, stop line adjustment, inability to correct errors, etc., to improve production efficiency, precision Background pattern, thick three-dimensional effect
- Summary
- Abstract
- Description
- Claims
- Application Information
AI Technical Summary
Problems solved by technology
Method used
Image
Examples
Embodiment Construction
[0051] like figure 1 As shown, the present embodiment provides a screen printing production line for graphic coded steel plates, including the following equipment: an uncoiler 1, used to uncoil the crimped steel strip, and trim the steel strip; a sewing machine 2, used to The front and rear steel strips after the uncoiler 1 is uncoiled are connected together to ensure the continuity of the process after replacing the steel coils; the first tension roller 3 is used to make the steel strips stitched by the sewing machine 2 run smoothly; The sleeve 4 is used to ensure that the process section does not stop when the uncoiler 1 is uncoiled and the sewing machine 2 is stitched; the second tension roller 5 is used to make the steel strip wound out of the inlet looper 4 run smoothly; The roller coating equipment assembly 6 is two groups, which are used for the background color roller coating before the steel strip is screen printed (here, it should be noted that the roller coating equ...
PUM
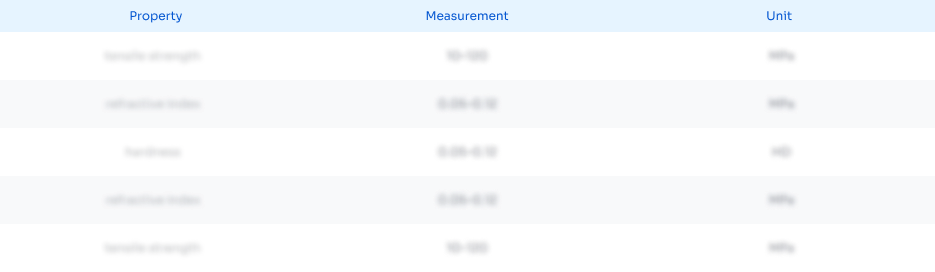
Abstract
Description
Claims
Application Information

- Generate Ideas
- Intellectual Property
- Life Sciences
- Materials
- Tech Scout
- Unparalleled Data Quality
- Higher Quality Content
- 60% Fewer Hallucinations
Browse by: Latest US Patents, China's latest patents, Technical Efficacy Thesaurus, Application Domain, Technology Topic, Popular Technical Reports.
© 2025 PatSnap. All rights reserved.Legal|Privacy policy|Modern Slavery Act Transparency Statement|Sitemap|About US| Contact US: help@patsnap.com