Rolling device for forming of copper alloy flat wires
A copper alloy and flat wire technology, applied in the direction of metal rolling, etc., can solve the problems of large size fluctuation, blurred surface of copper alloy flat wire, affecting electroplating and surface quality, etc. The effect of cost reduction
- Summary
- Abstract
- Description
- Claims
- Application Information
AI Technical Summary
Problems solved by technology
Method used
Image
Examples
Embodiment Construction
[0018] figure 1 It is a structural schematic diagram of a rolling device used for forming copper alloy flat wires according to the present invention. The rolling device used for forming flat copper alloy wire rods includes a pay-off mechanism, and the round wire blank 3 released from the pay-off mechanism passes through the first group of rolling mills 4, the first group of synchronous tension mechanisms 17, and the second group of rolling mills in sequence. 4. The second group of synchronous tension mechanism 17 and the third group of rolling mills 4 are finally rolled into the flat wire 13 of the target size, and the flat wire 13 is taken up through the wire take-up machine 14, and the described rolling mill 4 is powered by the electric control system 20; Rolling mill 4 comprises roll bracket 12 and upper roll 10 and lower roll 11 that are positioned at the top of roll bracket 12, and rolling mill bracket 12 is welded into box-type structure by metal material, and roll brack...
PUM
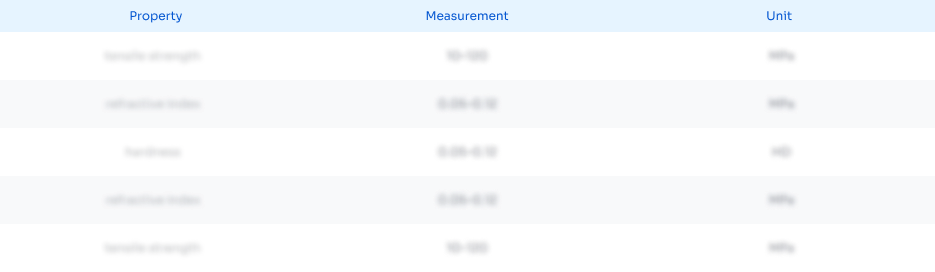
Abstract
Description
Claims
Application Information

- Generate Ideas
- Intellectual Property
- Life Sciences
- Materials
- Tech Scout
- Unparalleled Data Quality
- Higher Quality Content
- 60% Fewer Hallucinations
Browse by: Latest US Patents, China's latest patents, Technical Efficacy Thesaurus, Application Domain, Technology Topic, Popular Technical Reports.
© 2025 PatSnap. All rights reserved.Legal|Privacy policy|Modern Slavery Act Transparency Statement|Sitemap|About US| Contact US: help@patsnap.com