Metal bar rolling production line
A metal bar and production line technology, applied in metal rolling and other directions, can solve the problems of low rolling speed, large temperature drop of metal bars, scratches and even bending, etc., to improve rolling speed, compact unit structure, reduce Effect of rolling stock temperature drop
- Summary
- Abstract
- Description
- Claims
- Application Information
AI Technical Summary
Problems solved by technology
Method used
Image
Examples
Embodiment Construction
[0014] The present invention will be further described below in conjunction with the accompanying drawings and specific embodiments.
[0015] Such as figure 1 , figure 2 , image 3 As shown, the metal bar rolling production line includes: at least two longitudinally arranged rolling mill rows, each row of rolling mill rows includes at least two horizontal three-roll Y-shaped rolling mills, that is, all rolling mills The row-type three-roller Y-type rolling mills in the row are horizontally arranged into at least two rows of rolling units; each row of rolling mills is driven by a transmission device consisting of an electric motor and a reduction box. In this embodiment, the metal The bar rolling production line includes: two longitudinally arranged rolling mill rows, each row of rolling mill rows is provided with three row-type three-roll Y-shaped rolling mills, that is, the metal bar rolling production line includes six row-type Three-roll Y-rolling mills 3, 31, 32, 4, 41...
PUM
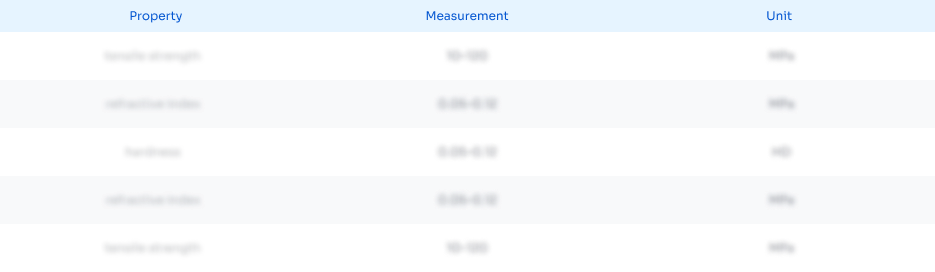
Abstract
Description
Claims
Application Information

- R&D
- Intellectual Property
- Life Sciences
- Materials
- Tech Scout
- Unparalleled Data Quality
- Higher Quality Content
- 60% Fewer Hallucinations
Browse by: Latest US Patents, China's latest patents, Technical Efficacy Thesaurus, Application Domain, Technology Topic, Popular Technical Reports.
© 2025 PatSnap. All rights reserved.Legal|Privacy policy|Modern Slavery Act Transparency Statement|Sitemap|About US| Contact US: help@patsnap.com