External-pressure resistant carbon fiber high-pressure pipe
A technology of carbon fiber and high-pressure pipes, applied in the chemical industry, can solve the problems of ineffectiveness, high temperature and high pressure resistance, waste of materials, etc., and achieve the effect of light weight and waste reduction
- Summary
- Abstract
- Description
- Claims
- Application Information
AI Technical Summary
Problems solved by technology
Method used
Image
Examples
Embodiment 1
[0019] The rubber compounding raw material that comprises the following parts by weight ratio; Bisphenol A diglycidyl ether, 1800 parts; 6360 trimethylol propane glycidyl ether, 170 parts; Methyl tetrahydrophthalic anhydride, 1700 parts; 2.4.6-tri( 15 parts of dimethylaminomethyl) phenol; fully stir evenly for substitution.
[0020] Prepare the above raw materials and put them into the rubber tank of the winding machine to replace them. The carbon fiber is infiltrated by the rubber tank and made into a product on the winding machine; start curing and heating up. The curing temperature is that the product is placed in the curing furnace and placed on a rotating tooling Rotate at a rate of one to two revolutions per minute.
[0021] Specific steps are as follows:
[0022] Start heating up from room temperature to 60 degrees Celsius for 3 hours;
[0023] Heat up to 100 degrees Celsius for 3 hours;
[0024] Heat up to 140 degrees Celsius for 2 hours;
[0025] Heat up to 160 de...
Embodiment 2
[0031] The rubber compounding raw material that comprises the following parts by weight ratio; Bisphenol A diglycidyl ether, 2100 parts; 6360 trimethylolpropane glycidyl ether, 200 parts; Methyltetrahydrophthalic anhydride, 1500 parts; 2.4.6-tri( 12 parts of dimethylaminomethyl) phenol; fully stir evenly for substitution.
[0032] Prepare the above raw materials and put them into the rubber tank of the winding machine to replace them. The carbon fiber is infiltrated by the rubber tank and made into a product on the winding machine; start curing and heating up. The curing temperature is that the product is placed in the curing furnace and placed on a rotating tooling Rotate at a rate of one to two revolutions per minute.
[0033] Specific steps are as follows:
[0034] Start heating up from room temperature to 60 degrees Celsius for 3 hours;
[0035] Heat up to 100 degrees Celsius for 3 hours;
[0036] Heat up to 140 degrees Celsius for 2 hours;
[0037] Heat up to 160 degr...
Embodiment 3
[0043] Containing the following rubber compounding materials in parts by weight: E51 bisphenol A diglycidyl ether, 2000 parts; 6360 trimethylolpropane glycidyl ether, 200 parts; methyl tetrahydrophthalic anhydride, 1700 parts; (Dimethylaminomethyl) phenol 12 parts, stir well and evenly substitute.
[0044] Prepare the above raw materials and put them into the rubber tank of the winding machine to replace them. The carbon fiber is infiltrated by the rubber tank and made into a product on the winding machine; start curing and heating up. The curing temperature is that the product is placed in the curing furnace and placed on a rotating tooling Rotate at a rate of one to two revolutions per minute.
[0045] Specific steps are as follows:
[0046] Start heating up from room temperature to 60 degrees Celsius for 3 hours;
[0047] Heat up to 100 degrees Celsius for 3 hours;
[0048] Heat up to 140 degrees Celsius for 2 hours;
[0049] Heat up to 160 degrees Celsius for 4 hours; ...
PUM
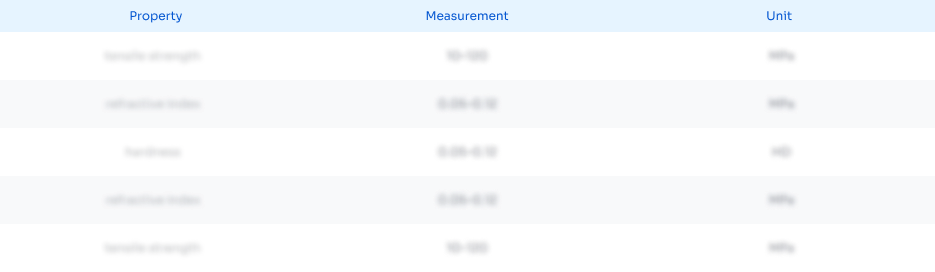
Abstract
Description
Claims
Application Information

- R&D Engineer
- R&D Manager
- IP Professional
- Industry Leading Data Capabilities
- Powerful AI technology
- Patent DNA Extraction
Browse by: Latest US Patents, China's latest patents, Technical Efficacy Thesaurus, Application Domain, Technology Topic, Popular Technical Reports.
© 2024 PatSnap. All rights reserved.Legal|Privacy policy|Modern Slavery Act Transparency Statement|Sitemap|About US| Contact US: help@patsnap.com