Cu-Ni alloy electro-polishing method used for EBSD test
An electrolytic polishing, cu-ni technology, applied in the preparation of test samples, etc., can solve problems such as the inability to obtain diffraction patterns
- Summary
- Abstract
- Description
- Claims
- Application Information
AI Technical Summary
Problems solved by technology
Method used
Image
Examples
example 1
[0028] The RD-ND section of the Cu-Ni alloy billet sample was mechanically polished first, and then ultrasonically cleaned with acetone for 5 minutes after mechanical polishing. Then carry out electrolytic polishing to the Cu-Ni alloy ingot sample that mechanical polishing is good, and cathode material is metal platinum sheet, this Cu-Ni alloy electrolytic polishing liquid (concentration is the concentrated H of 98%) 2 SO 4 : concentrated H with a concentration of 85% 3 PO 4 :H 2 O=1.5:2.5:1.8) As for the low-speed stirring on the magnetic stirrer (1 revolution / second), the AC voltage during electrolytic polishing is 15V, the electrolytic polishing temperature is 25°C, and the electrolytic polishing time is 20s. After the electropolished samples were ultrasonically cleaned in acetone, they were dried and stored for EBSD testing. figure 2 It is the EBSD grain boundary diagram of the Cu-Ni alloy ingot.
example 2
[0030] The RD-ND section of the Cu-Ni alloy sample with a cold-rolled deformation of 95% was mechanically polished first, and then ultrasonically cleaned with acetone for 5 minutes after mechanical polishing. Then electropolish the Cu-Ni alloy sample with 95% cold-rolled deformation after mechanical polishing, and the cathode material is metal platinum sheet. 2 SO 4 : concentrated H with a concentration of 85% 3 PO 4 :H 2 O=1:3:1.8) As for the low-speed stirring on the magnetic stirrer (1 revolution / second), the AC voltage during electrolytic polishing is 10V, the electrolytic polishing temperature is 15°C, and the electrolytic polishing time is 10s. After the electropolished samples were ultrasonically cleaned in acetone, they were dried and stored for EBSD testing. image 3 (a) is the EBSD grain boundary diagram of the RD-ND section of the Cu-Ni alloy base strip with a cold rolling deformation of 95%.
example 3
[0032] The RD-ND section of the Cu-Ni alloy sample with a cold-rolled deformation of 98.5% was mechanically polished first, and then ultrasonically cleaned with acetone for 5 minutes after mechanical polishing. Then electrolytic polishing is carried out to the Cu-45at.%Ni alloy sample whose cold-rolled deformation of mechanical polishing is 98.5%, and the cathode material is a metal platinum sheet. h 2 SO 4 : concentrated H with a concentration of 85% 3 PO 4 :H 2 O=1:3:1.8) As for the low-speed stirring on the magnetic stirrer (0.5 rev / s), the AC voltage during electrolytic polishing is 8V, the electrolytic polishing temperature is 10°C, and the electrolytic polishing time is 10s. After the electropolished samples were ultrasonically cleaned in acetone, they were dried and stored for EBSD testing. image 3 (b) is the EBSD grain boundary diagram of the RD-ND section of the Cu-Ni alloy base strip with a cold rolling deformation of 98.5%.
PUM
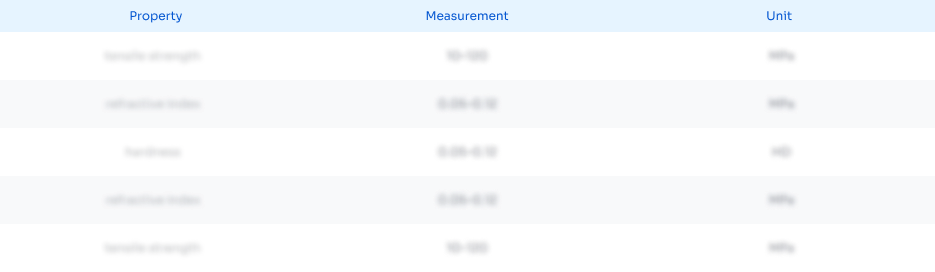
Abstract
Description
Claims
Application Information

- R&D
- Intellectual Property
- Life Sciences
- Materials
- Tech Scout
- Unparalleled Data Quality
- Higher Quality Content
- 60% Fewer Hallucinations
Browse by: Latest US Patents, China's latest patents, Technical Efficacy Thesaurus, Application Domain, Technology Topic, Popular Technical Reports.
© 2025 PatSnap. All rights reserved.Legal|Privacy policy|Modern Slavery Act Transparency Statement|Sitemap|About US| Contact US: help@patsnap.com