Servo control system of four-axis full-automatic tin soldering robot
A servo control system, fully automatic technology, applied in the direction of program control manipulators, manipulators, manufacturing tools, etc., can solve the problems of poor anti-interference ability, poor soldering iron head, increased mechanical noise, etc., to achieve enhanced anti-interference ability and shorten development The effect of short cycle times and increased processing speed
- Summary
- Abstract
- Description
- Claims
- Application Information
AI Technical Summary
Problems solved by technology
Method used
Image
Examples
Embodiment Construction
[0021] The preferred embodiments of the present invention will be described in detail below in conjunction with the accompanying drawings, so that the advantages and features of the present invention can be more easily understood by those skilled in the art, so as to define the protection scope of the present invention more clearly.
[0022] Digital signal processing chips (DSP) have fast computing capabilities, among which TMS320F2812 is a fixed-point 32-bit DSP chip on the C2000 platform launched by TI Company of the United States. The DSP operating clock can reach 150MHz, the processing performance can reach 150MIPS, each instruction cycle is 6.67ns, and the IO port is abundant, which is sufficient for the general application of users. It has 12-bit 0~3.3v AD conversion and 128k×16-bit on-chip FLASH and 18K × 16-bit SRAM, the general application system does not need to expand the memory. It has an independent arithmetic logic unit and powerful digital signal processing capa...
PUM
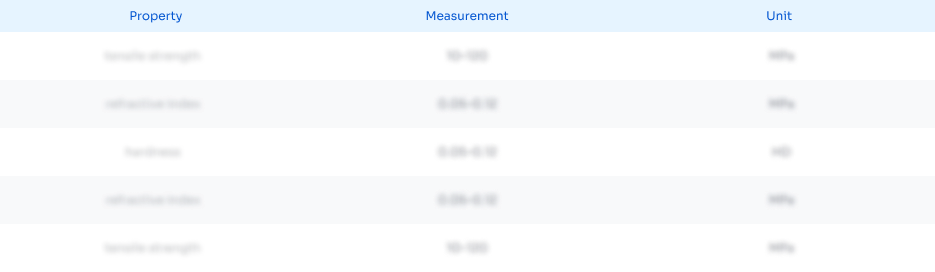
Abstract
Description
Claims
Application Information

- R&D
- Intellectual Property
- Life Sciences
- Materials
- Tech Scout
- Unparalleled Data Quality
- Higher Quality Content
- 60% Fewer Hallucinations
Browse by: Latest US Patents, China's latest patents, Technical Efficacy Thesaurus, Application Domain, Technology Topic, Popular Technical Reports.
© 2025 PatSnap. All rights reserved.Legal|Privacy policy|Modern Slavery Act Transparency Statement|Sitemap|About US| Contact US: help@patsnap.com