Method for producing vanadium pentoxide and by-product manganese sulfate from by using coal vanadium ore and pyrolusite together
A technology of vanadium pentoxide and stone coal vanadium, applied in the field of joint production of vanadium pentoxide by-product manganese sulfate from stone coal vanadium ore and pyrolusite, can solve the problem of large pollution of vanadium extraction from stone coal, low metal recovery rate, vanadium Solve problems such as low leaching rate, achieve strong promotion and application value, improve metal recovery rate, and reduce energy consumption
- Summary
- Abstract
- Description
- Claims
- Application Information
AI Technical Summary
Problems solved by technology
Method used
Image
Examples
Embodiment 1
[0022] Follow the steps of crushing ball milling and sieving, batching, acid leaching, oxidation, ion exchange adsorption, ion exchange desorption, vanadium precipitation, calcination, ion exchange tail water purification and impurity removal, evaporation and concentration, etc., in the batching process, select Stone coal with a vanadium grade of 1.0% is used as raw material, and the stone coal is blended at a ratio of 1:1 between the amount of vanadium contained in the stone coal vanadium ore and the amount of manganese dioxide contained in the pyrolusite. The leaching rate of vanadium in coal is 95%, the recovery rate of vanadium is 86%, the leaching rate of manganese in pyrolusite is 98%, and the total recovery rate of manganese is 91%.
Embodiment 2
[0024] Follow the steps of crushing ball milling and sieving, batching, acid leaching, oxidation, ion exchange adsorption, ion exchange desorption, vanadium precipitation, calcination, ion exchange tail water purification and impurity removal, evaporation and concentration, etc., in the batching process, select Stone coal with a vanadium grade of 1.5% is used as raw material, and the ratio of the amount of vanadium contained in the stone coal vanadium ore to the amount of manganese dioxide contained in the pyrolusite is 1:1. The leaching rate of vanadium in coal is 96%, the recovery rate of vanadium is 87%, the leaching rate of manganese in pyrolusite is 97%, and the total recovery rate of manganese is 90%.
Embodiment 3
[0026] Follow the steps of crushing ball milling and sieving, batching, acid leaching, oxidation, ion exchange adsorption, ion exchange desorption, vanadium precipitation, calcination, ion exchange tail water purification and impurity removal, evaporation and concentration, etc., in the batching process, select Stone coal with 1.0% vanadium grade is used as raw material, and the ratio of the amount of vanadium contained in the stone coal vanadium ore to the amount of manganese dioxide contained in the pyrolusite is 1:2. The leaching rate of vanadium in coal is 98%, the recovery rate of vanadium is 89%, the leaching rate of manganese in pyrolusite is 96%, and the total recovery rate of manganese is 88%.
[0027] In order to make the objectives, technical solutions, and advantages of the present invention clearer, the following further describes the present invention in detail with reference to the accompanying drawings and embodiments. It should be understood that the specific emb...
PUM
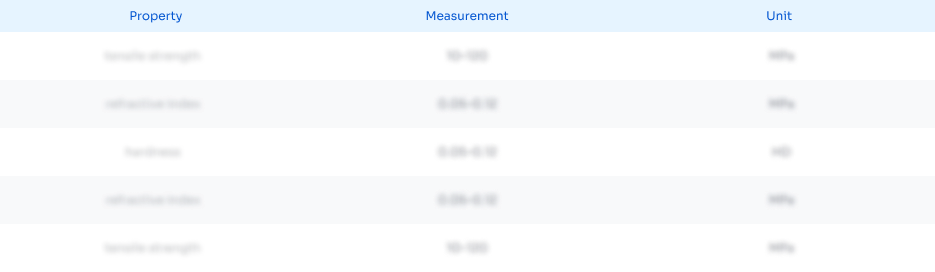
Abstract
Description
Claims
Application Information

- R&D
- Intellectual Property
- Life Sciences
- Materials
- Tech Scout
- Unparalleled Data Quality
- Higher Quality Content
- 60% Fewer Hallucinations
Browse by: Latest US Patents, China's latest patents, Technical Efficacy Thesaurus, Application Domain, Technology Topic, Popular Technical Reports.
© 2025 PatSnap. All rights reserved.Legal|Privacy policy|Modern Slavery Act Transparency Statement|Sitemap|About US| Contact US: help@patsnap.com