Device and method for testing forming property of sheet material under effect of fluid pressure
A testing device and sheet forming technology, applied in the field of sheet hydroforming, can solve the problems of inability to achieve dynamic sealing, difficult real-time testing and accurate evaluation, etc., and achieve the effects of easy implementation, simple and reliable structure, and mature manufacturing technology
- Summary
- Abstract
- Description
- Claims
- Application Information
AI Technical Summary
Problems solved by technology
Method used
Image
Examples
specific Embodiment approach 1
[0026]Specific implementation mode one: the following combination figure 1 , figure 2 , image 3 and Figure 4 This embodiment will be specifically described. The device includes a thick-walled cylinder 11, which is a circular thick-walled cylinder, on which is provided with an injection hole 4 communicating with the fluid medium cavity 10, and injects the fluid into the fluid medium cavity 10 through the injection hole 4 during operation. Inject the fluid medium; the circular inner wall of the thick-walled cylinder 11 is smooth and connected up and down, and the thick-walled cylinder 11 is respectively connected with the upper end cover 13 and the lower end cover 9 by sealing threads, and the upper end cover 13 and the lower end cover 9 are respectively connected with the upper clamping Part 1 and the lower clamping part 7 are connected in the form of a cylindrical through hole to form a complete dynamic sealed cavity. The upper end cover 13 and the inner wall of the smoo...
specific Embodiment approach 2
[0027] Specific implementation mode two: the following combination figure 1 , figure 2 , image 3 and Figure 5 This embodiment will be specifically described. The difference between this embodiment and the first embodiment is that the gauge width of the aluminum alloy plate sample 3 is 5 mm, and the other components and structures are the same as those of the first embodiment.
specific Embodiment approach 3
[0028] Embodiment 3: The difference between this embodiment and Embodiment 1 is that the material of the plate sample is selected as a magnesium alloy, and other components and structures are the same as Embodiment 1.
PUM
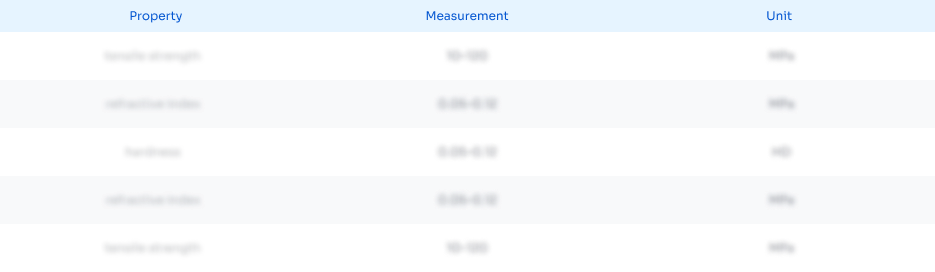
Abstract
Description
Claims
Application Information

- Generate Ideas
- Intellectual Property
- Life Sciences
- Materials
- Tech Scout
- Unparalleled Data Quality
- Higher Quality Content
- 60% Fewer Hallucinations
Browse by: Latest US Patents, China's latest patents, Technical Efficacy Thesaurus, Application Domain, Technology Topic, Popular Technical Reports.
© 2025 PatSnap. All rights reserved.Legal|Privacy policy|Modern Slavery Act Transparency Statement|Sitemap|About US| Contact US: help@patsnap.com