Double-interface card production process
A dual-interface card and production process technology, which is applied to record carriers, instruments, computer parts, etc. used in machines, can solve the problems of cumbersome groove milling process, module scratches, and large loss, so as to achieve simple process and improve production efficiency. and quality effects
- Summary
- Abstract
- Description
- Claims
- Application Information
AI Technical Summary
Problems solved by technology
Method used
Image
Examples
Embodiment Construction
[0032] The present invention will be further described below in conjunction with the accompanying drawings and specific embodiments.
[0033] according to figure 2 , the production process of the dual-interface card of the present invention is as follows: obtain PVC sheets through plate-making design, film plate-making, and printing, obtain the winding layer 2c through picking and PVC winding, and make it through lamination, lamination and punching processes Card 2, the milling machine mills out the coil 1 and mills off the paint layer on the surface of the coil 1 to expose the copper; after that, the module is tinned, milled flat, and glue is prepared, and the module is punched into small modules 5, and the copper wire of the coil on the card 2 4 (same as coil 1) apply solder paste 8 on the surface, manually fix the small module 5 in the card milling groove frame 3, and then perform hot pressing, electrical performance testing, personalization of card data, inspection, packa...
PUM
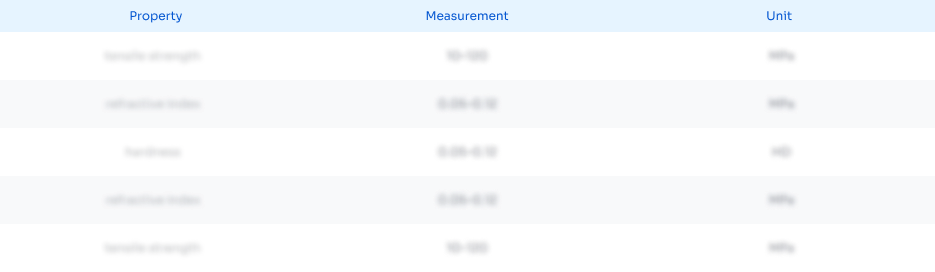
Abstract
Description
Claims
Application Information

- R&D
- Intellectual Property
- Life Sciences
- Materials
- Tech Scout
- Unparalleled Data Quality
- Higher Quality Content
- 60% Fewer Hallucinations
Browse by: Latest US Patents, China's latest patents, Technical Efficacy Thesaurus, Application Domain, Technology Topic, Popular Technical Reports.
© 2025 PatSnap. All rights reserved.Legal|Privacy policy|Modern Slavery Act Transparency Statement|Sitemap|About US| Contact US: help@patsnap.com