Method for converter steel tapping alloying molten steel component evening
A technology of molten steel composition and steel alloy, applied in the direction of manufacturing converters, etc., can solve the problems of uneven composition of molten steel, loss of its own dynamic conditions, etc.
- Summary
- Abstract
- Description
- Claims
- Application Information
AI Technical Summary
Problems solved by technology
Method used
Image
Examples
Embodiment 1
[0034] This embodiment is used for refining Q235B type steel, whose standard carbon content is 0.12-0.20% by weight, silicon content is 0.15-0.30% by weight, and manganese content is 0.30-0.70% by weight.
[0035] 140t of semi-steel (its composition is: 3.60% by weight C, 0.032% by weight of Mn, 0.03% by weight of V, 0.010% by weight of S, 0.077% by weight of P, and the balance is Fe) is blended into a 120t converter furnace, and then passed through oxygen The gun blows oxygen into it, and the oxygen supply intensity is 2.86-3.79Nm 3 / t·min. Based on the total amount of oxygen blown in, when the oxygen blowing amount is 21% (the time is about 3 minutes after the start of oxygen blowing, and the total oxygen blowing time is 14 minutes), add the first batch of slagging agents (including composite slagging The agent composition is mainly 50% by weight of SiO 2and 15% by weight of CaO, the composition of the lime slagging agent is mainly 86% by weight of CaO) 4200kg (composite s...
Embodiment 2
[0039] This embodiment is used for refining HRB400 type steel, whose standard carbon content is 0.19-0.25% by weight, silicon content is 0.50-0.80% by weight, manganese content is 1.30-1.60% by weight, and vanadium content is 0.04-0.12% by weight.
[0040] According to the method of embodiment 1, molten steel is produced, and the molten steel obtained after blowing is tapped into a ladle, and the total tapping time is 4-7 minutes. When the tapping amount accounted for 20% by weight of the total tapping amount, 160kg of pitch coke was added, and when the tapping amount accounted for 30% by weight of the total tapping amount, the addition of pitch coke was completed. 1-2 minutes from the completion of adding pitch coke, when the tapping amount accounted for 55% by weight of the total tapping amount, Si-Mn alloy 2700kg, Si-Ca-Ba alloy 300kg, Fe-Si alloy 340kg, V-Fe 95kg of the alloy is added to the ladle, and when the tapping amount accounts for 80% by weight of the total tapping...
Embodiment 3
[0043] This embodiment is used for refining B-shaped steel, whose standard carbon content is 0.17-0.23% by weight, silicon content is 0.17-0.37% by weight, and manganese content is 0.35-0.65% by weight.
[0044] According to the method of embodiment 1, molten steel is produced, and the molten steel obtained after blowing is tapped into a ladle, and the total tapping time is 4-7 minutes. When the tapping amount accounted for 19% by weight of the total tapping amount, 160kg of quasi-graphite was added, and when the tapping amount accounted for 29% by weight of the total tapping amount, the addition of quasi-graphite was completed. Add 1-2 minutes from graphite-like, when tapping amount accounts for 52% by weight of total tapping amount, Si-Mn alloy 570kg, Si-Ca-Ba alloy 300kg, Fe-Si alloy 60kg are added ladle, in When the tapping amount accounts for 75% by weight of the total tapping amount, the addition of the alloy is completed. After adding graphite, when the molten steel in...
PUM
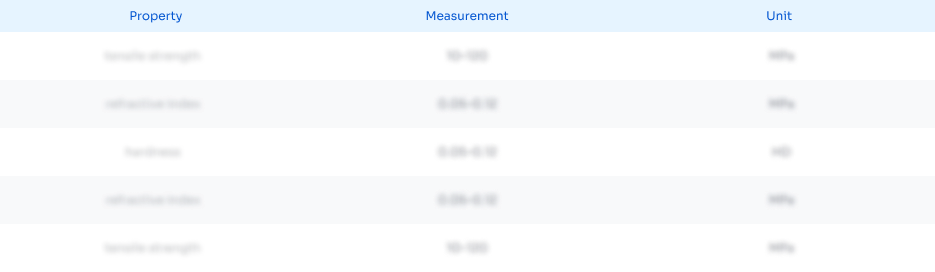
Abstract
Description
Claims
Application Information

- R&D
- Intellectual Property
- Life Sciences
- Materials
- Tech Scout
- Unparalleled Data Quality
- Higher Quality Content
- 60% Fewer Hallucinations
Browse by: Latest US Patents, China's latest patents, Technical Efficacy Thesaurus, Application Domain, Technology Topic, Popular Technical Reports.
© 2025 PatSnap. All rights reserved.Legal|Privacy policy|Modern Slavery Act Transparency Statement|Sitemap|About US| Contact US: help@patsnap.com