Production method of graph code steel plate integrating roller painting printing and silk-screen printing into whole
一种丝网印刷、生产方法的技术,应用在丝网印刷、丝网印刷机、印刷机械的通用零件等方向,能够解决停线调整、不能钢板辊涂转印、速度不一致等问题,达到精确底色花纹、提高生产效率的效果
- Summary
- Abstract
- Description
- Claims
- Application Information
AI Technical Summary
Problems solved by technology
Method used
Image
Examples
Embodiment 1
[0044] Such as figure 1 As shown, this embodiment provides a method for producing a two-color pattern color steel plate, which includes the following steps:
[0045] A. Prepare the steel strip to be printed. In this step, the uncoiler is used to uncoil the steel coil and carry out edge trimming, and the uncoiled steel strip is stitched by a sewing machine;
[0046] B. Using the first roller coating unit to carry out a roller coating transfer to the steel strip to be printed;
[0047] C. After a certain period of time, the second roller coating unit is used to carry out the second roller coating transfer on the steel strip, and the second roller coating transfer and the first roller coating transfer form the specific surface of the steel strip to be printed. background pattern;
[0048] D. placing the steel strip forming the background pattern on the printing table for screen printing, so as to form a pattern code of a specific shape on the steel strip with a specific backgro...
Embodiment 2
[0064] This embodiment provides a method for producing a patterned steel plate that integrates roller coating printing and screen printing. This production method is a deformation based on the production method provided in Example 1, and it is the only difference from Example 1. The difference is that the methods of leveling the steel strips are different. In this embodiment, the specific method of leveling the steel strip is as follows: a plurality of through holes are provided on the printing platform corresponding to the placement position of the steel strip, and a plurality of through holes are provided at the bottom of the printing platform. There is a fan, and when leveling, the fan sucks air through the through hole, thereby forming a negative pressure in the gap space formed between the steel belt and the printing table, and then pressing the steel belt to the The printing table realizes the leveling of the steel strip.
Embodiment 3
[0066] In this embodiment, a structure of the roller coating transfer unit used in steps B and C in Embodiment 1 and Embodiment 2 is provided. For the specific structure, see figure 2 , the roller coating unit includes feeding equipment 1 for providing coating; suction roller 2, whose peripheral surface is connected with the feeding equipment 1, and has an image area formed when filling with the coating on the peripheral surface a plurality of depressions; the rubber coating roller 3, whose peripheral surface is connected with the suction roller 2, is used to accept the image area formed by the coating on the coating roller 3, and transfer the image area onto the steel plate; also includes a first scraper 4, installed on the first scraper bracket, contacting the suction roller 2 at a specific angle, for scraping off the paint outside the image area of the suction roller 2 The second scraper 5, installed on the second scraper bracket, is in contact with the coating rolle...
PUM
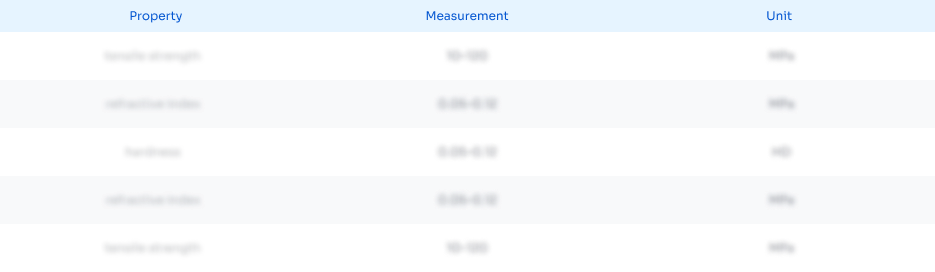
Abstract
Description
Claims
Application Information

- R&D
- Intellectual Property
- Life Sciences
- Materials
- Tech Scout
- Unparalleled Data Quality
- Higher Quality Content
- 60% Fewer Hallucinations
Browse by: Latest US Patents, China's latest patents, Technical Efficacy Thesaurus, Application Domain, Technology Topic, Popular Technical Reports.
© 2025 PatSnap. All rights reserved.Legal|Privacy policy|Modern Slavery Act Transparency Statement|Sitemap|About US| Contact US: help@patsnap.com