Hex-blade conical ball milling cutter used for machining impeller deep hole
A ball milling cutter and deep hole technology, applied in milling cutters, metal processing equipment, manufacturing tools, etc., can solve problems such as difficulty in ensuring the radius R of the ball head of the cutter, affecting product development progress, and prolonging the cycle of blisk addition. Achieve the effects of reducing labor costs, increasing the number of regrinding, and increasing the qualified rate of regrinding
- Summary
- Abstract
- Description
- Claims
- Application Information
AI Technical Summary
Problems solved by technology
Method used
Image
Examples
Embodiment 1
[0031] A six-edged conical ball milling cutter for impeller deep hole machining, which is composed of a coaxial and integral tool handle 1, a tool bar 2, and a cutting edge 3 arranged at the front end of the tool bar 2; it meets the following requirements:
[0032] The six-edged conical ball milling cutter for impeller deep hole machining requires the following:
[0033] When the tool diameter is 10mm, the axial dimension of tool holder 1 is 16mm; when the tool diameter is 16mm, the axial dimension of tool holder 1 is 20mm;
[0034] The shank 1 taper of the tool is 4°;
[0035] The rake angle of the cutter is 5°, the relief angle is 2°, the helix angle is 20°, the blade width is 0.2mm, and the effective length of the cutter head is 35mm.
[0036] Taking a typical large axial-flow integral impeller made of titanium alloy as an example, without reducing the feed rate per tooth of the tool, two cutting edges are added to increase the processing feed rate and the processing effic...
Embodiment 2
[0083] The content of this embodiment is basically the same as that of Embodiment 1, the difference is that:
[0084] The six-edged conical ball milling cutter for deep hole machining of the impeller is used for fine milling of the casing cavity of the high-temperature alloy casing. Because it is a difficult-to-machine material, the material has high hardness, high viscosity, poor thermal conductivity, and processing variability; The parts are specifically GH4169 nickel-based superalloy, the processing part is the cavity wall of the casing shell, and the transfer radius is 5mm. After rough milling and semi-finishing, the machining allowance is 0.3mm.
[0085] In the finishing milling process, a six-edged milling cutter is used to remove the remaining 0.3mm allowance. The parameters of the finishing milling process require:
[0086] Tool diameter 10mm; blade number Z=6; maximum aspect ratio 1.5×D; depth of cut A p =0.3mm, cutting speed V c =70m / min; Feed per tooth F z =0.1mm...
Embodiment 3
[0088] The content of this embodiment is basically the same as that of Embodiment 1, the difference is that:
[0089] The six-edged conical ball milling cutter for deep hole machining of the impeller is used for finish milling of the stainless steel casing. , The machining allowance is 0.3mm.
[0090] In the finishing milling process, a six-edged milling cutter is used to remove the remaining 0.3mm allowance. The parameters of the finishing milling process require:
[0091] Tool diameter 10mm; blade number Z=6; maximum aspect ratio 1.5×D; depth of cut A p =0.5mm, cutting speed V c =140m / min; Feed per tooth F z =0.1mm; speed n=4500RPM; feed F=2700mm / min.
PUM
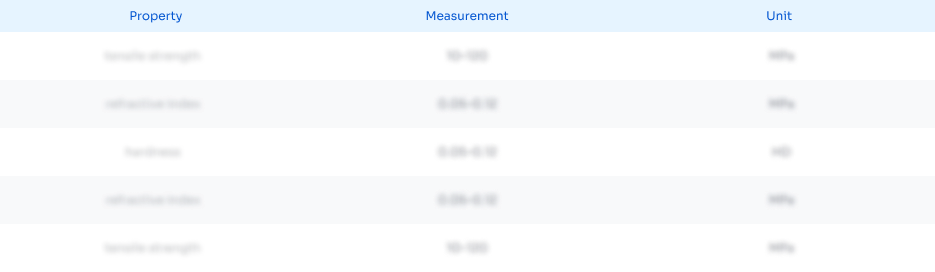
Abstract
Description
Claims
Application Information

- R&D
- Intellectual Property
- Life Sciences
- Materials
- Tech Scout
- Unparalleled Data Quality
- Higher Quality Content
- 60% Fewer Hallucinations
Browse by: Latest US Patents, China's latest patents, Technical Efficacy Thesaurus, Application Domain, Technology Topic, Popular Technical Reports.
© 2025 PatSnap. All rights reserved.Legal|Privacy policy|Modern Slavery Act Transparency Statement|Sitemap|About US| Contact US: help@patsnap.com