Screen printing conductive printing ink composition and preparation method thereof
A conductive ink and screen printing technology, applied in ink, household utensils, applications, etc., can solve the problems of long curing time, high brittleness of cured film, high curing temperature, etc., and achieve stable electrical performance, good printing performance and high mechanical strength Effect
- Summary
- Abstract
- Description
- Claims
- Application Information
AI Technical Summary
Problems solved by technology
Method used
Image
Examples
Embodiment 1
[0038] A screen printing conductive ink composition of the present invention, the conductive ink composition comprises the following components in parts by mass (see Table 1 below):
[0039] Flake silver powder Ferro SF70A 100 parts;
[0040] Alicyclic trifunctional epoxy resin TDE-85 11.20 parts;
[0041] Epoxy resin latent curing agent (Shenzhen Chuang Chou Applied Materials Co., Ltd. ICAM-8409) 0.33 parts;
[0042] 3.36 parts of ternary vinyl acetate resin;
[0043] 10.26 parts of isophorone;
[0044] 20.55 parts of dipropylene glycol methyl ether;
[0045] 5.13 parts of 150# solvent oil;
[0046] 5.60 parts of core-shell structure rubber micro-nano particle modified epoxy resin;
[0047] Thixotropic agent BYK-410 (BYK company) 1.00 parts;
[0048] Antioxidant SRE-701 (Serui Technology, USA) 0.80 parts; and
[0049] Defoamer SRE-2022A (Serui Technology, USA) 0.80 parts.
[0050] The preparation method of the screen printing conductive ink composition of the present ...
Embodiment 2
[0059] A screen printing conductive ink composition of the present invention, the conductive ink composition comprises the following components in parts by mass (see Table 1 below):
[0060] Flake silver powder Ferro SF70A 100 parts;
[0061] Epoxy resin DER-331 (Dow chemical bisphenol A epoxy resin) 9.97 parts;
[0062] Epoxy resin latent curing agent (ICAM-8403) (Shenzhen Chuang Chou Applied Materials Co., Ltd.) 2.09 parts;
[0063] PVB (B-98) (Yiston Chemical New Materials Co., Ltd.) 2.98 copies;
[0064] DBE 5.94 copies;
[0065] 23.73 parts of dipropylene glycol methyl ether;
[0066] 5.94 parts of 150# solvent oil;
[0067] Nitrile rubber modified epoxy resin 861340 (Shenzhen Jiadida Chemical Co., Ltd.) 3.99 parts;
[0068] Thixotropic agent BYK-410 (BYK company) 0.90 parts;
[0069] Antioxidant SRE-701 (Serui Technology, USA) 0.80 parts; and
[0070] Defoamer SRE-2022A (Serui Technology, USA) 0.50 parts.
[0071] The preparation method of the screen printing con...
Embodiment 3
[0080] A screen printing conductive ink composition of the present invention, the conductive ink composition comprises the following mass ratio components (see Table 1 below):
[0081] Flake silver powder Ferro SF70A 100 parts;
[0082] Epoxy resin DER-331 8.82 parts;
[0083] Epoxy resin latent curing agent (Shenzhen ICAM-8403) 3.14 parts;
[0084] 3.17 parts of ternary vinyl acetate resin;
[0085] 9.46 parts of isophorone;
[0086] 18.92 parts of dipropylene glycol methyl ether;
[0087] 150# solvent oil 4.73 parts;
[0088] Nitrile rubber modified epoxy resin 861340 (Shenzhen Jiadida Chemical Co., Ltd.) 4.41 parts;
[0089] Thixotropic agent BYK-410 (BYK company) 1.10 parts;
[0090] Antioxidant SRE-701 (Serui Technology, USA) 0.80 parts; and
[0091] Defoamer SRE-2022A (Serui Technology, USA) 0.80 parts.
[0092] The preparation method of the screen printing conductive ink composition of the present embodiment comprises the following steps:
[0093] 1. Preparation ...
PUM
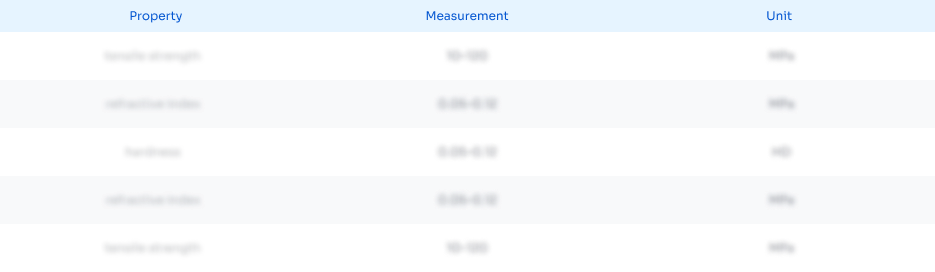
Abstract
Description
Claims
Application Information

- R&D
- Intellectual Property
- Life Sciences
- Materials
- Tech Scout
- Unparalleled Data Quality
- Higher Quality Content
- 60% Fewer Hallucinations
Browse by: Latest US Patents, China's latest patents, Technical Efficacy Thesaurus, Application Domain, Technology Topic, Popular Technical Reports.
© 2025 PatSnap. All rights reserved.Legal|Privacy policy|Modern Slavery Act Transparency Statement|Sitemap|About US| Contact US: help@patsnap.com