Biomass heavy-oil hydrocracking catalyst and preparation method thereof
A biomass heavy oil and hydrocracking technology, which is applied in the direction of physical/chemical process catalysts, molecular sieve catalysts, chemical instruments and methods, etc., can solve the problems of high acid value, high oxygen content and high viscosity of biomass oil, and achieve improved The effect of uniformity
- Summary
- Abstract
- Description
- Claims
- Application Information
AI Technical Summary
Problems solved by technology
Method used
Examples
Embodiment 1
[0022] Mix 43 grams of modified Y molecular sieve, 17 grams of SBA-15, and 7 grams of molybdenum trioxide evenly, add 4ml of concentrated nitric acid and appropriate amount of water, stir evenly and place for 2 hours, then dry at 120°C for 12 hours, and grind into powder.
[0023] Mix 20 grams of German-made SB alumina, 5 grams of kaolin, and 3 grams of magnesium oxide evenly, place them in a palladium chloride solution containing 1.0 grams of Pd metal for impregnation, and dry them at 120°C for 12 hours after immersion; then place Immerse in a nickel acetate solution containing 5.0 grams of Ni metal, dry at 120°C for 12 hours after immersion for 12 hours, and finally grind it into powder.
[0024] Mix the solid powder obtained in the above two steps evenly, add 6ml of concentrated nitric acid and appropriate amount of water, add 2 grams of safflower powder, stir and mix evenly, extrude into Φ2mm cylindrical strips on the extruder, and heat up to 120°C at a speed of 2°C / Min Dr...
Embodiment 2
[0026] Mix 30 grams of modified Y molecular sieve, 20 grams of SBA-15, and 5 grams of molybdenum trioxide evenly, add 6ml of concentrated hydrochloric acid and appropriate amount of water, stir evenly and place for 2 hours, then dry at 120°C for 12 hours, and grind into powder.
[0027] Mix 30 grams of German-made SB alumina, 4 grams of kaolin, and 4 grams of magnesium oxide evenly, place them in a rhodium chloride solution containing 0.8 grams of Rh metal for impregnation, and dry at 120°C for 12 hours after immersion; then place It is impregnated in a nickel acetate solution containing 6.0 grams of Ni metal, dried at 120° C. for 12 hours after immersion for 12 hours, and finally ground into powder.
[0028]Mix the solid powder obtained in the above two steps evenly, add 9ml of concentrated hydrochloric acid and appropriate amount of water, add 2 grams of safflower powder, stir and mix evenly, extrude into Φ2mm cylindrical strips on the extruder, and heat up to 120°C at a spee...
Embodiment 3
[0030] Mix 40 grams of modified Y molecular sieve, 15 grams of SBA-15, and 6 grams of tungsten trioxide evenly, add 5ml of concentrated nitric acid and appropriate amount of water, stir evenly and place it for 2 hours, then dry it at 120°C for 12 hours, and grind it into powder.
[0031] Mix 25 grams of German SB alumina, 4 grams of kaolin, and 4 grams of boric acid evenly, and place them in a mixed solution of chloride containing 0.7 grams of Rh metal for impregnation. After soaking for 12 hours, dry at 120°C for 12 hours; Ni metal was impregnated in a nickel acetate solution of 5.0 g, dried at 120°C for 12 hours after impregnated for 12 hours, and finally ground into powder.
[0032] Mix the solid powder obtained in the above two steps evenly, add 9ml of concentrated nitric acid and appropriate amount of water, add 2 grams of scallop powder, stir and mix evenly, extrude into Φ2mm cylindrical strips on the extruder, and heat up to 120°C at a speed of 2°C / Min Dry at constant t...
PUM
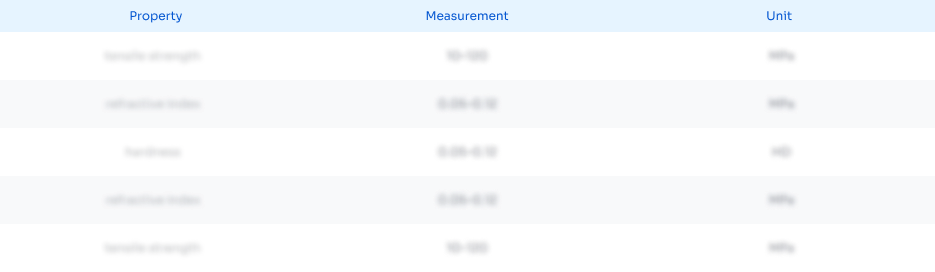
Abstract
Description
Claims
Application Information

- R&D
- Intellectual Property
- Life Sciences
- Materials
- Tech Scout
- Unparalleled Data Quality
- Higher Quality Content
- 60% Fewer Hallucinations
Browse by: Latest US Patents, China's latest patents, Technical Efficacy Thesaurus, Application Domain, Technology Topic, Popular Technical Reports.
© 2025 PatSnap. All rights reserved.Legal|Privacy policy|Modern Slavery Act Transparency Statement|Sitemap|About US| Contact US: help@patsnap.com