Microbead-like dry granules, as well as preparation method and application thereof
A technology of dry grains and microbeads is applied to the field of forming glaze substances on the surface of the green body, which can solve the problems of single processing method, poor fluidity of dry grains, unsatisfactory glazing effect, etc. , the effect of good liquidity
- Summary
- Abstract
- Description
- Claims
- Application Information
AI Technical Summary
Problems solved by technology
Method used
Image
Examples
Embodiment 1
[0041] The preparation of embodiment 1 microbead shape dry grain
[0042] Quartz, potassium feldspar, albite, dolomite, heavy calcium, talc, zircon, borax, zinc oxide and cerium oxide are respectively ball milled to 200 mesh, mixed, fired at 1530-1540°C for 1.5-2 hours, The frit is obtained through water quenching, and the frit is composed of the following components by weight:
[0043]
[0044]
[0045] The frit is made into bead-shaped dry particles A by flame flotation method in the glass microsphere manufacturing device. The flame temperature is controlled at about 900°C. The particle size range of micro-bead-shaped dry particles A is 60-170 mesh, and the production rate is 70%. ,Such as figure 2 As shown, the surface of microbead-shaped dry particle A is a spherical surface.
Embodiment 2
[0046] The preparation of embodiment 2 microbeads dry grain
[0047] Quartz, potassium feldspar, albite, dolomite, heavy calcium, zircon, boric acid, and zinc oxide are ball-milled to 200 mesh respectively, mixed, fired at 1530-1540°C for 1.5-2 hours, and quenched in water to obtain molten block, and then dried and crushed to 100-200 mesh, that is, common dry granules, which are composed of the following components by weight:
[0048]
[0049] Ordinary dry granules are made into bead-shaped dry granules B by flame flotation in the glass microsphere manufacturing device. The flame temperature is controlled at about 860°C. The particle size of micro-beaded dry granules B is 100-200 mesh, and the production rate is 95%. ,Such as figure 2 Shown, the surface of microbead-shaped dry particle B is a spherical surface.
Embodiment 3
[0050] Embodiment 3 screen printing prepares dry grain glaze ceramic tile
[0051] Use the 32T screen plate with the pattern to print the prepared glaze paste on the glazed tiles, and then fire them to obtain dry glazed tiles. The decorative patterns are three-dimensional and the effect is rich and colorful.
[0052] The glaze slurry for screen printing includes the following components by weight:
[0053] Lithographic printing ink 100 parts
[0054] 260 parts of microbead dry granule B.
PUM
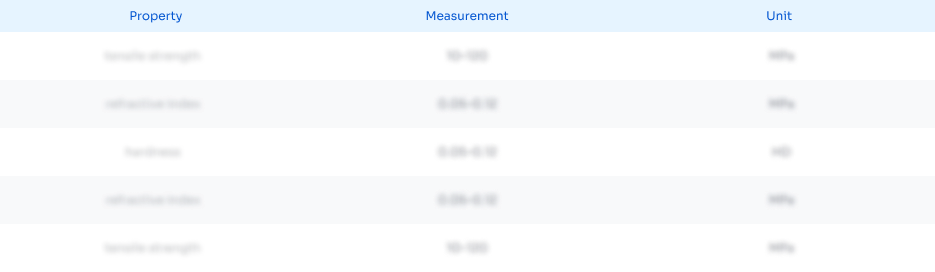
Abstract
Description
Claims
Application Information

- Generate Ideas
- Intellectual Property
- Life Sciences
- Materials
- Tech Scout
- Unparalleled Data Quality
- Higher Quality Content
- 60% Fewer Hallucinations
Browse by: Latest US Patents, China's latest patents, Technical Efficacy Thesaurus, Application Domain, Technology Topic, Popular Technical Reports.
© 2025 PatSnap. All rights reserved.Legal|Privacy policy|Modern Slavery Act Transparency Statement|Sitemap|About US| Contact US: help@patsnap.com