Phase-changed heat insulation polyolefin foam material and preparation method thereof
A technology of polyolefin foam and polyolefin resin, which is applied in the field of phase change thermal insulation polyolefin foam material and its preparation, to achieve the effect of improving sustainability
- Summary
- Abstract
- Description
- Claims
- Application Information
AI Technical Summary
Problems solved by technology
Method used
Examples
Embodiment 1
[0040] Example 1: Preparation of Phase Change Microcapsules
[0041] (1) Mix 40kg of n-tetradecane and 2kg of sodium dodecylbenzene sulfonate, and emulsify into an emulsion in a high-speed emulsifier. The speed of the high-speed emulsifier is 1000r / min, and the emulsification time is 5min;
[0042] (2) Add 20kg of melamine-formaldehyde prepolymer to the emulsion, stir evenly, adjust the pH value to 3.5 with acetic acid, react at 70°C for 0.5h, and stir at a speed of 500 r / min;
[0043] (3) Raise the temperature to 90°C, continue the reaction for 1 hour, and stir at a speed of 500 r / min.
[0044] After steps (1) and (2), phase change microcapsules with n-tetradecane as the capsule core and melamine-formaldehyde resin as the single-layer capsule wall can be prepared; through steps (1) to (3) can be prepared A phase-change microcapsule with n-tetradecane as the core and melamine-formaldehyde resin as the multi-layered wall was produced.
Embodiment 2
[0045] Example 2: Preparation of Phase Change Microcapsules
[0046] (1) Mix 10kg of paraffin wax and 6kg of Tween emulsifier, emulsify into an emulsion under a high-speed emulsifier, the speed of the high-speed emulsifier is 3000r / min, and the emulsification time is 5min;
[0047] (2) Add 60kg of urea-formaldehyde prepolymer into the emulsion, stir evenly, and let it stand for 2 hours. During this period, keep stirring at a stirring speed of 2500 r / min. ;
[0048] (3) Add 1 kg of urea-formaldehyde resin curing agent ammonium chloride, stir evenly, adjust the pH value to 2-3 with acetic acid, react at 80°C for 1 hour, and stir at a speed of 2500 r / min;
[0049] (4) Raise the temperature to 90°C, continue the reaction for 1 hour, and stir at 2500 r / min.
[0050] Phase change microcapsules with paraffin as the core and urea-formaldehyde resin as the single-layer capsule wall can be prepared through steps (1) to (3); Phase-change microcapsules with capsule walls.
Embodiment 3
[0051] Example 3: Preparation of Phase Change Microcapsules
[0052] (1) Take 10kg of gelatin and 25kg of gum arabic, prepare 15% aqueous solutions respectively, and raise the temperature to 55°C;
[0053] (2) Take 30 kg of n-octadecane and 5 kg of sorbitan fatty acid ester, mix them, and emulsify them into an emulsion under a high-speed emulsifier, the speed of the high-speed emulsifier is 1000r / min, and the emulsification time is 5 minutes;
[0054] (3) Add the gelatin solution, adjust the pH value to 4.0 with citric acid, stir evenly, keep the system temperature at 55°C, and react for 2 hours;
[0055] (4) Add the prepared gum arabic melt, adjust the pH value to 3.5 with citric acid, stir evenly, keep the system temperature at 55°C, and react for 5 hours.
[0056] Phase-change microcapsules with n-octadecane as the capsule core and gelatin as the single-layer capsule wall can be prepared through steps (1) to (3); Gum is a phase-change microcapsule with multi-layer capsule...
PUM
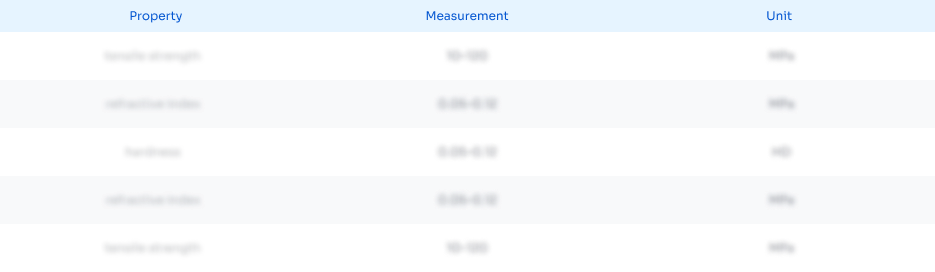
Abstract
Description
Claims
Application Information

- R&D
- Intellectual Property
- Life Sciences
- Materials
- Tech Scout
- Unparalleled Data Quality
- Higher Quality Content
- 60% Fewer Hallucinations
Browse by: Latest US Patents, China's latest patents, Technical Efficacy Thesaurus, Application Domain, Technology Topic, Popular Technical Reports.
© 2025 PatSnap. All rights reserved.Legal|Privacy policy|Modern Slavery Act Transparency Statement|Sitemap|About US| Contact US: help@patsnap.com