Forming method of air gap in interconnection layer
A technology of air gap and interconnection layer, applied in the direction of electrical components, semiconductor/solid-state device manufacturing, circuits, etc., can solve the problems of poor performance of semiconductor integrated circuits, achieve the effect of reducing RC effect, improving performance, and uniform width
- Summary
- Abstract
- Description
- Claims
- Application Information
AI Technical Summary
Problems solved by technology
Method used
Image
Examples
Embodiment Construction
[0042] As mentioned in the background, the prior art semiconductor integrated circuit has poor performance after air gaps are formed in the interconnection layer.
[0043] After doing your research, go ahead and refer to Figure 5 The inventors found that the reason for the poor performance of the semiconductor integrated circuit in the prior art is that there are more interlayer dielectric layers 103 between two adjacent trenches, resulting in a higher effective K value in the interconnection layer.
[0044] The inventors have found that if a sacrificial layer is formed by oxidizing the sidewall of the trench 107 without using a deposition process, the process steps can be reduced. Please refer to figure 2 , removing the patterned photoresist layer 105 by using an ashing process (please refer to figure 2 ) while oxidizing the interlayer dielectric layer 103 on the sidewall of the trench 107 to form a sacrificial layer, and then filling the trench 107 with conductive metal ...
PUM
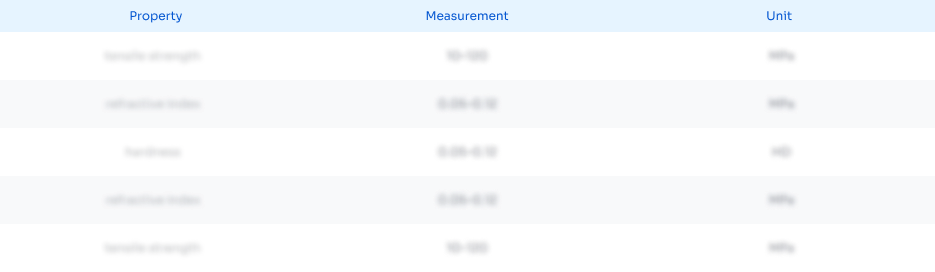
Abstract
Description
Claims
Application Information

- R&D
- Intellectual Property
- Life Sciences
- Materials
- Tech Scout
- Unparalleled Data Quality
- Higher Quality Content
- 60% Fewer Hallucinations
Browse by: Latest US Patents, China's latest patents, Technical Efficacy Thesaurus, Application Domain, Technology Topic, Popular Technical Reports.
© 2025 PatSnap. All rights reserved.Legal|Privacy policy|Modern Slavery Act Transparency Statement|Sitemap|About US| Contact US: help@patsnap.com