Coating type composite material for dry type transformer and preparation method thereof
A technology of dry-type transformers and composite materials, applied in chemical instruments and methods, lamination, lamination devices, etc., can solve the problems of composite materials such as heat resistance limitation, overall performance decline, and limited adsorption performance, so as to ensure insulation performance , prolong the service life, and the overall smooth and uniform effect
- Summary
- Abstract
- Description
- Claims
- Application Information
AI Technical Summary
Problems solved by technology
Method used
Image
Examples
Embodiment 1
[0043] 1. After the polyester film is impregnated with an epoxy system adhesive, it is combined with both sides of the polyester fiber non-woven fabric to form a five-layer composite material A;
[0044] 2. Prepare high temperature resistant epoxy resin coating solution according to the following weight ratio:
[0045] 604 epoxy resin: 24%; 6101 epoxy resin: 13%; 128 epoxy resin: 2%; 1411 phenolic resin: 13%; 4,4ˊ-diaminodiphenylsulfone: 6%; acetone: 42%.
[0046] 3. Dip-coat the above-mentioned high-temperature-resistant epoxy resin coating solution with the prepared five-layer composite material A, so that the high-temperature-resistant epoxy resin is coated on the upper and lower organic or inorganic fiber paper layers to form a seven-layer composite material B. Bake at 140°C for 2.5 minutes, and cool to room temperature to obtain the product.
[0047] The corresponding technical indicators of this product are shown in Table 1:
[0048]Table 1 The technical indicators of ...
Embodiment 2
[0051] 1. After the polyimide film is impregnated with the polyurethane system adhesive, it is composited with both sides of the polyester fiber non-woven fabric to form a five-layer composite material A;
[0052] 2. Prepare high temperature resistant epoxy resin coating solution according to the following weight ratio:
[0053] 604 epoxy resin: 28%; 6101 epoxy resin: 13%; 128 epoxy resin: 0%; 1411 phenolic resin: 13%; 4,4ˊ-diaminodiphenylsulfone: 4%; acetone: 42%.
[0054] 3. Dip-coat the above-mentioned high-temperature-resistant epoxy resin coating solution with the prepared five-layer composite material A, so that the high-temperature-resistant epoxy resin is coated on the upper and lower organic or inorganic fiber paper layers to form a seven-layer composite material B. Bake at 135°C for 3.5 minutes, and cool to room temperature to obtain the product.
[0055] The corresponding technical indicators of this product are shown in Table 2:
[0056] The technical index of th...
Embodiment 3
[0059] 1. After the polyimide film is impregnated with the polyesterimide system adhesive, it is combined with both sides of the polyaramid fiber paper to form a five-layer composite material A;
[0060] 2. Prepare high temperature resistant epoxy resin coating solution according to the following weight ratio:
[0061] 604 epoxy resin: 21%; 6101 epoxy resin: 15%; 128 epoxy resin: 5%; 1411 phenolic resin: 15%; 4,4ˊ-diaminodiphenylsulfone: 5%; acetone: 39%.
[0062] 3. Dip-coat the above-mentioned high-temperature-resistant epoxy resin coating solution with the prepared five-layer composite material A, so that the high-temperature-resistant epoxy resin is coated on the upper and lower organic or inorganic fiber paper layers to form a seven-layer composite material B. Bake at 145°C for 2 minutes, and cool to room temperature to obtain the product.
[0063] The corresponding technical indicators of this product are shown in Table 3:
[0064] The technical index of the composite ...
PUM
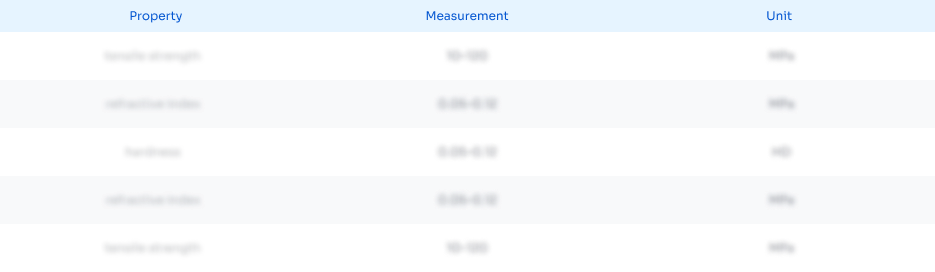
Abstract
Description
Claims
Application Information

- R&D
- Intellectual Property
- Life Sciences
- Materials
- Tech Scout
- Unparalleled Data Quality
- Higher Quality Content
- 60% Fewer Hallucinations
Browse by: Latest US Patents, China's latest patents, Technical Efficacy Thesaurus, Application Domain, Technology Topic, Popular Technical Reports.
© 2025 PatSnap. All rights reserved.Legal|Privacy policy|Modern Slavery Act Transparency Statement|Sitemap|About US| Contact US: help@patsnap.com