Method for producing arene by utilizing methanol
A technology for methanol and aromatic hydrocarbons, which is applied in the production of bulk chemicals, chemical instruments and methods, and hydrocarbon production from oxygen-containing organic compounds, etc. The effect of carbon power
- Summary
- Abstract
- Description
- Claims
- Application Information
AI Technical Summary
Problems solved by technology
Method used
Image
Examples
Embodiment 1
[0023] a) Take 100g silicon aluminum ratio SiO 2 / Al 2 o 3 Add 20 ZSM-5 molecular sieve raw powder to 600g of 1.5mol / L sodium hydroxide solution, stir at 30°C for 30min, filter and wash with water, and then dry the filter cake at 100°C for 8h.
[0024] b) Take 80 g of molecular sieves dried in step a), mix them with 400 g of 5% ammonium nitrate solution, heat at 80°C for 2h, filter and wash with water, then dry the filter cake at 100°C for 8h, and roast at 500°C for 4h to obtain type H ZSM-5 molecular sieve.
[0025] c) Take 20g of the HZSM-5 molecular sieve prepared in the step b), and mix it with 58g of pseudo-boehmite and 2.0g of turmeric powder. Dilute nitric acid was added to the mixture, kneaded evenly, extruded, dried at 110°C for 12 hours, and calcined at 600°C for 6 hours to prepare a catalyst carrier.
[0026] d) Dissolve 2.7g of zinc nitrate in 15g of water, add 20g of the catalyst carrier prepared in step c), dry at 110°C for 12h, and roast at 600°C for 4h to p...
Embodiment 2
[0029] a) Take 100g silicon aluminum ratio SiO 2 / Al 2 o 3 Add 200 ZSM-5 molecular sieve raw powder to 600 g of 0.1 mol / L potassium hydroxide solution, stir at 80 °C for 240 min, filter and wash with water, and then dry the filter cake at 100 °C for 10 h.
[0030] b) Take 80 g of molecular sieves dried in step a), mix them with 400 g of 5% ammonium nitrate solution, heat at 80°C for 2h, filter and wash with water, then dry the filter cake at 120°C for 8h, and roast at 550°C for 4h to obtain type H ZSM-5 molecular sieve.
[0031] c) Take 20g of HZSM-5 molecular sieve prepared in step b), 30g of pseudo-boehmite, and 1.0g of starch and mix them evenly. Dilute nitric acid was added to the mixture, kneaded evenly, extruded, dried at 100°C for 12 hours, and calcined at 580°C for 5 hours to prepare a catalyst carrier.
[0032] d) Dissolve 1.0 g of zinc sulfate in 28 g of water, add 40 g of the catalyst carrier prepared in step c), dry at 120°C for 8 hours, and roast at 600°C for ...
Embodiment 3
[0035] a) Take 100g silicon aluminum ratio SiO 2 / Al 2 o 3 Add 100 ZSM-5 molecular sieve raw powder to 500 g of potassium hydroxide solution with a concentration of 0.5 mol / L, stir at 80 °C for 120 min, filter and wash with water, and then dry the filter cake at 120 °C for 2 h.
[0036] b) Take 80 g of molecular sieves dried in step a), mix them with 400 g of 5% ammonium nitrate solution, heat at 80°C for 2h, filter and wash with water, then dry the filter cake at 100°C for 16h, and roast at 580°C for 3h to obtain type H ZSM-5 molecular sieve.
[0037] c) Take 38g of the HZSM-5 molecular sieve prepared in step b), 10g of pseudo-boehmite, and 1.5g of celadon powder and mix them evenly. Dilute nitric acid was added to the mixture, kneaded evenly, extruded, dried at 100°C for 12 hours, and calcined at 550°C for 5 hours to prepare a catalyst carrier.
[0038] d) Dissolve 3.3g of zinc chloride in 20g of water, add 20g of the catalyst carrier prepared in step c), dry at 110°C fo...
PUM
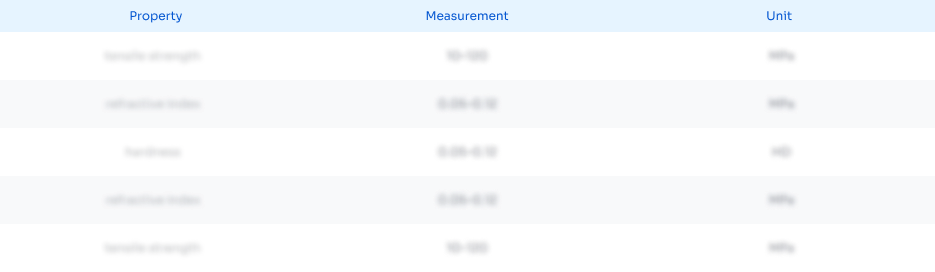
Abstract
Description
Claims
Application Information

- R&D Engineer
- R&D Manager
- IP Professional
- Industry Leading Data Capabilities
- Powerful AI technology
- Patent DNA Extraction
Browse by: Latest US Patents, China's latest patents, Technical Efficacy Thesaurus, Application Domain, Technology Topic, Popular Technical Reports.
© 2024 PatSnap. All rights reserved.Legal|Privacy policy|Modern Slavery Act Transparency Statement|Sitemap|About US| Contact US: help@patsnap.com