Preparation method of catalytic cracking catalyst
A catalytic cracking and catalyst technology, used in catalytic cracking, physical/chemical process catalysts, molecular sieve catalysts, etc., can solve the problems of difficulty in recycling, complex composition, and high water content, and achieve recycling, product quality stability, and dosage reduction. Effect
- Summary
- Abstract
- Description
- Claims
- Application Information
AI Technical Summary
Problems solved by technology
Method used
Image
Examples
preparation example Construction
[0013] The preparation method of described catalytic cracking catalyst according to the present invention comprises the following steps:
[0014] (1) The catalyst filter residue, NaY molecular sieve gel, kaolin and binder are mixed and slurried, and the resulting slurry is spray-dried to obtain microspheres, wherein, relative to 100 parts by weight of the microspheres, the catalyst The amount of the filter residue on a dry basis is 10-60 parts by weight, the amount of the NaY molecular sieve gel on a dry basis is 5-20 parts by weight, and the amount of kaolin on a dry basis is 20-70 parts by weight;
[0015] (2) Carrying out gas-phase crystallization of the microspheres obtained in step (1), and then roasting;
[0016] (3) The product obtained after roasting is mixed with directing agent, sodium silicate and sodium hydroxide, and subjected to hydrothermal crystallization, and then the product obtained after hydrothermal crystallization is filtered, washed and dried to obtain N...
Embodiment 1
[0040] This example is used to illustrate the preparation method of the catalytic cracking catalyst of the present invention.
[0041] (1) Preparation of NaY molecular sieve
[0042] 2.8kg (dry basis) kaolin, 0.48kg NaY molecular sieve gel (in dry basis, SiO 2 :Al 2 o 3 :Na 2 The molar ratio of O is 8.4:1:2.6) and 0.4kg catalyst filter residue (on a dry basis, SiO 2 :Al 2 o 3 :Na 2 O:Fe 2 o 3 : Re 2 o 3 :Cl - : SO 4 2- The weight ratio is 62.5: 21.56: 5.8: 0.24: 1.26: 1.27: 6.24) mixed, and water and 1.3kg water glass (containing 20.03% by weight of SiO 2 , 6.39 wt% Na 2 (2, the balance being water), making a slurry with a solid content of 32% by weight, which was then spray-dried to obtain 4kg of spray microspheres A1.
[0043] The sprayed microspheres A1 were vapor-phase crystallized in a saturated water vapor atmosphere at 98°C for 24 hours, and then calcined in a muffle furnace at 600°C for 2 hours to obtain calcined microspheres B1.
[0044] Under stirrin...
Embodiment 2
[0052] This example is used to illustrate the preparation method of the catalytic cracking catalyst of the present invention.
[0053] (1) Preparation of NaY molecular sieve
[0054] 2.4kg (dry basis) kaolin, 0.48kg NaY molecular sieve gel (in dry basis, SiO 2 :Al 2 o 3 :Na 2 The molar ratio of O is 8.4:1:2.6) and 0.8kg catalyst filter residue (on a dry basis, SiO 2 :Al 2 o 3 :Na 2 O:Fe 2 o 3 : Re 2 o 3 :Cl - : SO 4 2- The weight ratio is 62.5: 21.56: 5.8: 0.24: 1.26: 1.27: 6.24) mixed, and water and 1.3kg water glass (containing 20.03% by weight of SiO 2 , 6.39 wt% Na 2 (2, the balance being water), making a slurry with a solid content of 32% by weight, which was then spray-dried to obtain 4kg of spray microspheres A2.
[0055] The sprayed microspheres A2 were vapor-phase crystallized in a saturated water vapor atmosphere at 100°C for 24 hours, and then calcined in a muffle furnace at 600°C for 2 hours to obtain calcined microspheres B2.
[0056] Under stirri...
PUM
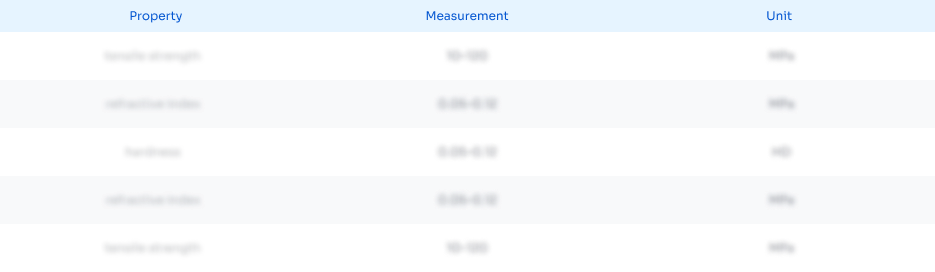
Abstract
Description
Claims
Application Information

- R&D
- Intellectual Property
- Life Sciences
- Materials
- Tech Scout
- Unparalleled Data Quality
- Higher Quality Content
- 60% Fewer Hallucinations
Browse by: Latest US Patents, China's latest patents, Technical Efficacy Thesaurus, Application Domain, Technology Topic, Popular Technical Reports.
© 2025 PatSnap. All rights reserved.Legal|Privacy policy|Modern Slavery Act Transparency Statement|Sitemap|About US| Contact US: help@patsnap.com