Method for preparing graphite fluoride at low temperature
A fluorinated graphite, low temperature technology, applied in the field of non-metallic materials, can solve the problems of high equipment requirements, high production risk, low fluorocarbon ratio of fluorinated graphite, etc., and achieve the effect of high purity
- Summary
- Abstract
- Description
- Claims
- Application Information
AI Technical Summary
Problems solved by technology
Method used
Examples
preparation example Construction
[0012] Preparation of absolute ethanol: Add 1L of 95% ethanol and 150g of quicklime to a 2L round-bottomed flask, shake well, plug it tightly with a rubber stopper and leave it overnight; add a condenser tube to the round-bottomed flask containing the overnight materials, and assemble Reflux device and heat reflux on the electric heating mantle for 2 hours; after the reflux is over, when the reaction system is slightly cooled, it is converted into a distillation device and heated by the electric heating mantle to distill anhydrous ethanol for use.
[0013] The graphite flakes, ferric fluoride and potassium hexafluoromanganate are put into a vacuum desiccator and vacuum dried for 8-12 hours for use.
Embodiment 1
[0015] After adding 100g flake graphite and 20g ferric fluoride into the dry reactor, feed nitrogen (in other embodiments, any inert gas can be fed into) to exhaust the air in the reactor, and then use a syringe to react under nitrogen flow. Inject 633mL of absolute ethanol and 143mL of bromine trifluoride in sequence, and stir at 25°C for 50 minutes; then obtain a solid substance by vacuum filtration, wash the solid substance repeatedly with water until the pH of the washing liquid is 7.0, then suction filter and vacuum dry Obtain graphite intercalation compound; 100g graphite intercalation compound and 175g potassium hexafluoromanganate are thoroughly mixed and put into a dry reactor, and nitrogen gas is passed into the reactor (in other embodiments, any Inert gas) until the air in the reactor is exhausted, inject 61mL antimony pentafluoride into the reactor with a syringe, then raise the temperature to the reaction temperature of 160°C, stop heating after 1.5h and cool natur...
Embodiment 2
[0017] After adding 100g flake graphite and 10g ferric fluoride into the dry reactor, feed nitrogen (in other embodiments, any inert gas can be fed into) to exhaust the air in the reactor, and then use a syringe to react under nitrogen flow. Inject 850mL of absolute ethanol and 90mL of bromine trifluoride in sequence, and stir at 25°C for 50 minutes; then obtain a solid substance by vacuum filtration, wash the solid substance repeatedly with water until the pH of the washing liquid is 7.0, then suction filter and vacuum dry Obtain graphite intercalation compound; 100g graphite intercalation compound and 150g potassium hexafluoromanganate are thoroughly mixed and put into a dry reactor, and nitrogen gas is passed into the reactor (in other embodiments, any Inert gas) until the air in the reactor is exhausted, inject 55mL antimony pentafluoride into the reactor with a syringe, then raise the temperature to the reaction temperature of 160°C, stop heating after 1.5h and cool natura...
PUM
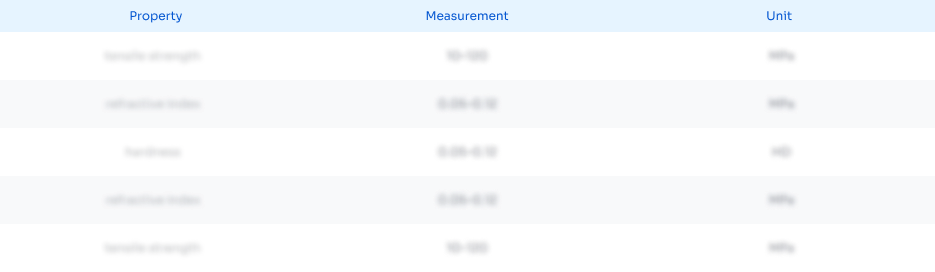
Abstract
Description
Claims
Application Information

- R&D
- Intellectual Property
- Life Sciences
- Materials
- Tech Scout
- Unparalleled Data Quality
- Higher Quality Content
- 60% Fewer Hallucinations
Browse by: Latest US Patents, China's latest patents, Technical Efficacy Thesaurus, Application Domain, Technology Topic, Popular Technical Reports.
© 2025 PatSnap. All rights reserved.Legal|Privacy policy|Modern Slavery Act Transparency Statement|Sitemap|About US| Contact US: help@patsnap.com