Preparation method of film adsorbing material
A technology for adsorbing materials and films, applied in chemical instruments and methods, other chemical processes, etc., can solve the problems of short service life, poor selectivity, and high price, and achieve the effects of reducing environmental damage, fast adsorption, and simple process.
- Summary
- Abstract
- Description
- Claims
- Application Information
AI Technical Summary
Problems solved by technology
Method used
Examples
example 1
[0015] (1) Pulverization: put the discarded plastic film into a pulverizer and pulverize it into plastic pieces;
[0016] (2) Cleaning: Add water to the crushed plastic sheet, the water volume submerges the plastic sheet, first add 10ppm chloroform, then add 30ppm gasoline, and ultrasonically wash for 30 minutes;
[0017] (3) Peeling: Pour the cleaned plastic sheet into the barrel, which contains 0.5M hydrochloric acid and 1.5M nitric acid solution, so that the metal on the plastic sheet is dissolved into the acid to realize the peeling of the plastic sheet and the metal;
[0018] (4) Filtration: decontamination and metal removal plastic sheets are separated from the solution;
[0019] (5) Drying: first dry at a constant temperature at 105°C, and then crack at an elevated temperature of 800°C under nitrogen protection;
[0020] (6) Dissolving: dissolving the cracked plastic sheet with dichloroethane solvent;
[0021] (7) Granulation: Wash with clean water, pick up and dry, t...
example 2
[0023] (1) Pulverization: put the discarded plastic film into a pulverizer and pulverize it into plastic pieces;
[0024] (2) Cleaning: Add water to the crushed plastic sheet, the water volume submerges the plastic sheet, first add 15ppm chloroform, then add 40ppm gasoline, and ultrasonically wash for 35 minutes;
[0025] (3) Peeling: Pour the cleaned plastic sheet into the barrel, which contains 0.5M hydrochloric acid and 1.5M nitric acid solution, so that the metal on the plastic sheet is dissolved into the acid to realize the peeling of the plastic sheet and the metal;
[0026] (4) Filtration: decontamination and metal removal plastic sheets are separated from the solution;
[0027] (5) Drying: first dry at a constant temperature at 105°C, and then crack at an elevated temperature of 800°C under nitrogen protection;
[0028] (6) Dissolving: dissolving the cracked plastic sheet with dichloroethane solvent;
[0029] (7) Granulation: Wash with clean water, pick up and dry, t...
example 3
[0031] (1) Pulverization: put the discarded plastic film into a pulverizer and pulverize it into plastic pieces;
[0032] (2) Cleaning: Add water to the crushed plastic sheet, the water volume submerges the plastic sheet, first add 20ppm chloroform, then add 50ppm gasoline, and ultrasonically wash for 45 minutes;
[0033] (3) Peeling: Pour the cleaned plastic sheet into the barrel, which contains 0.5M hydrochloric acid and 1.5M nitric acid solution, so that the metal on the plastic sheet is dissolved into the acid to realize the peeling of the plastic sheet and the metal;
[0034] (4) Filtration: decontamination and metal removal plastic sheets are separated from the solution;
[0035] (5) Drying: first dry at a constant temperature at 105°C, and then crack at an elevated temperature of 800°C under nitrogen protection;
[0036] (6) Dissolving: dissolving the cracked plastic sheet with dichloroethane solvent;
[0037] (7) Granulation: Wash with clean water, pick up and dry, t...
PUM
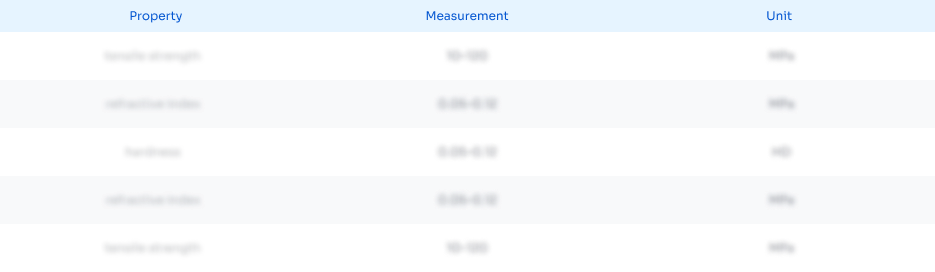
Abstract
Description
Claims
Application Information

- Generate Ideas
- Intellectual Property
- Life Sciences
- Materials
- Tech Scout
- Unparalleled Data Quality
- Higher Quality Content
- 60% Fewer Hallucinations
Browse by: Latest US Patents, China's latest patents, Technical Efficacy Thesaurus, Application Domain, Technology Topic, Popular Technical Reports.
© 2025 PatSnap. All rights reserved.Legal|Privacy policy|Modern Slavery Act Transparency Statement|Sitemap|About US| Contact US: help@patsnap.com