Control method of two-way direct current conversion device
A technology of bidirectional DC conversion and control method, which is applied in the field of control of bidirectional DC conversion devices, can solve problems such as complex circuits and poor phase shift of PWM driving waveforms, and achieve reduced interleaving number, simple design, and reduced current ripple Effect
- Summary
- Abstract
- Description
- Claims
- Application Information
AI Technical Summary
Problems solved by technology
Method used
Image
Examples
Embodiment Construction
[0036] The present invention will be described in detail below with reference to the accompanying drawings and examples.
[0037] Aiming at the classic independent PWM control strategy, the present invention proposes a complementary PWM control strategy. The complementary PWM control strategy is to simultaneously control the complementary conduction of the upper and lower switching tubes within a cycle Ts. When the current is large, it is equivalent to the independent PWM control strategy. When the current is small The Buck state and Boost state are switched within one switching cycle, thereby ensuring the current continuity when the current is small, so only one control system is needed to ensure control accuracy.
[0038] Moreover, for high-power occasions, the switching devices (power switching tubes, freewheeling diodes, and energy transfer inductors) of the bidirectional DC conversion device are subjected to high voltage and current stress, causing serious radiation and co...
PUM
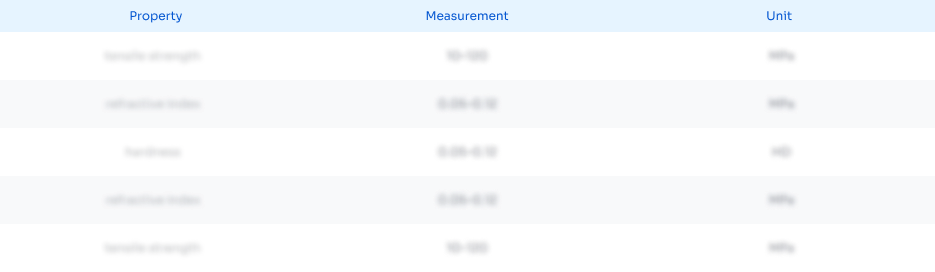
Abstract
Description
Claims
Application Information

- R&D
- Intellectual Property
- Life Sciences
- Materials
- Tech Scout
- Unparalleled Data Quality
- Higher Quality Content
- 60% Fewer Hallucinations
Browse by: Latest US Patents, China's latest patents, Technical Efficacy Thesaurus, Application Domain, Technology Topic, Popular Technical Reports.
© 2025 PatSnap. All rights reserved.Legal|Privacy policy|Modern Slavery Act Transparency Statement|Sitemap|About US| Contact US: help@patsnap.com