Method for pretreating raw polar plates for internal formation
A raw plate and pretreatment technology, applied in the direction of lead-acid battery electrodes, etc., can solve the problems of uneven dispersion of colloidal electrolyte, high temperature of battery acid addition, and poor state of separators, so as to improve capacity consistency and qualified capacity Efficiency, reduction of floating powder on the surface, relief of inconvenience
- Summary
- Abstract
- Description
- Claims
- Application Information
AI Technical Summary
Problems solved by technology
Method used
Image
Examples
Embodiment 1
[0024] Acid pickling treatment: Use low-density 1.08g / mL (25°C) dilute sulfuric acid to completely immerse the polar plates. The temperature of the dilute sulfuric acid should be 10°C, the positive plate immersion time is 80 minutes, and the negative plate immersion time is 40 minutes.
[0025] Secondary drying treatment: After the soaking time is completed, the electrode plate is taken and placed on the curing rack (the method is the same as the coating plate and placed on the curing rack), enter the drying room, and use temperature segmented drying, the first stage is 45℃× 3h, the second stage is 65℃×6h, and the third stage is 35℃×3h.
[0026] After the plate is dried, we sample the material content of the plate for testing. The material content of the plate before the above treatment is also analyzed:
[0027] Positive plate: 4 points are tested separately (refer to the distribution of test points figure 1 ), the results are shown in Table 1:
[0028] Table 1
[0029]
[0030] Nega...
Embodiment 2
[0065] Acid pickling treatment: The electrode plates are completely immersed in dilute sulfuric acid with a density of 1.18g / mL (25°C). The temperature of the dilute sulfuric acid is required to be 25°C, the immersion time of the positive plate is 60 minutes, and the immersion time of the negative plate is 30 minutes.
[0066] Secondary drying treatment: After the soaking time is completed, the electrode plate is taken and placed on the curing rack (the method is the same as the coating plate and placed on the curing rack), enter the drying room, and use temperature segmented drying, the first stage is 50℃× 3h, 75℃×6h for the second stage, 40℃×3h for the third stage.
[0067] After the plate is dried, we sample the material content of the plate for testing. The material content of the plate before the above treatment is also analyzed:
[0068] Positive plate: 4 points are tested separately (test points such as figure 1 Shown), the test results are shown in Table 5:
[0069] table 5
...
Embodiment 3
[0106] Acid immersion treatment: The electrode plates are completely immersed in dilute sulfuric acid with a density of 1.28g / mL (25°C). The temperature of the dilute sulfuric acid is 35°C, the immersion time of the positive plate is 40 minutes, and the immersion time of the negative plate is 20 minutes.
[0107] Secondary drying treatment: After the soaking time is completed, the plate is taken and placed on the curing rack (the method is the same as the coating plate and placed on the curing rack), enter the drying room, and use temperature segmented drying, the first stage is 55℃× 3h, the second stage is 85℃×6h, and the third stage is 45℃×3h.
[0108] After the plate is dried, we sample the material content of the plate for testing. The material content of the plate before the above treatment is also analyzed:
[0109] Positive plate: 4 points are tested separately (refer to the distribution of test points figure 1 ), the test results are shown in Table 9:
[0110] Table 9
[0111]...
PUM
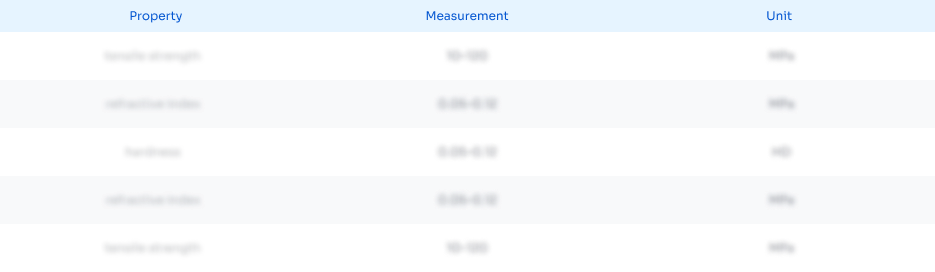
Abstract
Description
Claims
Application Information

- Generate Ideas
- Intellectual Property
- Life Sciences
- Materials
- Tech Scout
- Unparalleled Data Quality
- Higher Quality Content
- 60% Fewer Hallucinations
Browse by: Latest US Patents, China's latest patents, Technical Efficacy Thesaurus, Application Domain, Technology Topic, Popular Technical Reports.
© 2025 PatSnap. All rights reserved.Legal|Privacy policy|Modern Slavery Act Transparency Statement|Sitemap|About US| Contact US: help@patsnap.com