Device and method for measuring static rigidity of rolling linear guide rail pair
A technology of a linear guide rail pair and a measuring device, applied in the field of measurement, can solve the problems of influence of measurement accuracy, small load range, inconvenient operation, etc., and achieve the effects of good self-locking performance, improved measurement efficiency, and easy installation and adjustment.
- Summary
- Abstract
- Description
- Claims
- Application Information
AI Technical Summary
Problems solved by technology
Method used
Image
Examples
Embodiment Construction
[0016] The invention uses a servo motor to drive a trapezoidal screw to drive the loading nut to load the rolling linear guide rail pair. By changing the installation position of the guide rail pair and the type of fixture on the guide rail, three loading methods can be performed on the guide rail pair: vertical, deflection and pitch loading. The force sensor and the laser displacement sensor sample the load and deformation of the tested guide rail pair respectively. The force sensor is fixed on the loading nut and can rise and fall with it. The center position of the laser displacement sensor and the corresponding measurement of different loading methods Points are aligned vertically. By processing the collected load and displacement data, the static stiffness curve of the rolling linear guide can be drawn, so as to realize the experimental measurement of the static stiffness of the rolling linear guide, and the load range of the measurement is large, the versatility is strong...
PUM
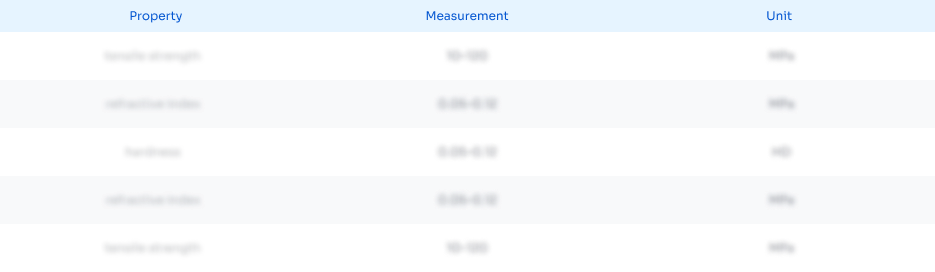
Abstract
Description
Claims
Application Information

- R&D
- Intellectual Property
- Life Sciences
- Materials
- Tech Scout
- Unparalleled Data Quality
- Higher Quality Content
- 60% Fewer Hallucinations
Browse by: Latest US Patents, China's latest patents, Technical Efficacy Thesaurus, Application Domain, Technology Topic, Popular Technical Reports.
© 2025 PatSnap. All rights reserved.Legal|Privacy policy|Modern Slavery Act Transparency Statement|Sitemap|About US| Contact US: help@patsnap.com