Integral casting process for reinforced concrete wastewater tank in predrilling engineering
A technology of reinforced concrete and monolithic pouring, which is applied in the direction of construction, building structure, and building material processing. It can solve the problems of affecting structural strength and durability, many stepped construction sections, and easy-to-distort formwork, and achieves easy construction time. Control and ensure the pouring size of the structure and enhance the effect of out-of-plane rigidity
- Summary
- Abstract
- Description
- Claims
- Application Information
AI Technical Summary
Problems solved by technology
Method used
Image
Examples
Embodiment 1
[0038] An integral pouring process for reinforced concrete wastewater pools in pre-drilling engineering, comprising the following steps:
[0039] a. Foundation and cushion construction: Excavate the foundation pit, confirm that the bearing capacity of the foundation meets the design requirements, and pour the concrete cushion;
[0040] b. Manufacture and installation of steel bars: For production and installation on site, the overlapping length of steel bars should not be less than 40 times the diameter (mm) of steel bars, and the overlapping area of steel bars of the same section should not exceed 50% of the total area;
[0041] c. Formwork support: Bind the formwork into the shape of the concrete pool bottom and pool wall;
[0042] d. Concrete pouring: After completing the construction of steel bars and formwork, carry out concrete pouring construction. First pour the concrete at the bottom of the pool and the wall of the pool below 1m. The top of the pool wall is level an...
Embodiment 2
[0053] The invention first carries out the construction of the cushion layer of the wastewater pool, and then manufactures and installs steel bars for the pool bottom and the pool wall, forms and pours them.
[0054] The specific construction sequence is: measurement and setting-out, foundation and cushion construction → measurement and setting-out, bottom plate and pool wall (including water stop sheet) installation → supporting formwork → pouring waste water pool bottom plate and pool wall concrete with a height below 1.0m → at the After the initial setting of the first pouring concrete, immediately pour the rest of the pool wall concrete→remove the formwork→cure.
[0055] The second part of concrete pouring is generally carried out about 1 hour after the first pouring is completed, that is, before the final setting of the first part of concrete. The bottom of the pool and the wall of the pool are formed at one time. The time interval between the two parts of concrete pourin...
Embodiment 3
[0064] This embodiment is mainly to describe in detail the wooden formwork system and supporting formwork in the present invention.
[0065] The wooden formwork 1 is provided with a tie hole 3, and the double tension screw 5 with the water stop sheet 4 passes through the tie hole 3 through the wood formwork on one side of the wall 2, the wall 2 and the other side of the wall 2 in turn. The wooden formwork is fixed on the steel pipe.
[0066] The process of setting up the formwork is as follows:
[0067] Wood formwork construction is carried out in two steps. The first is the vertical formwork. At this time, attention should be paid to the position and fixation of the wooden formwork to ensure the structural size and the protective thickness of the concrete. In order to enhance the out-of-plane rigidity of the wooden formwork, prevent the thickness of the concrete wall from being deformed and meet the higher anti-seepage requirements, the wooden formwork on both sides of the ...
PUM
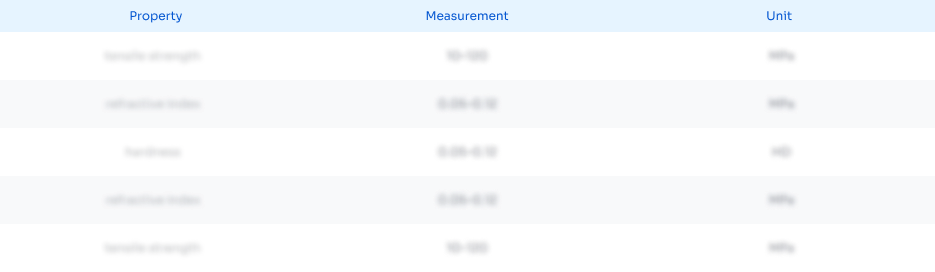
Abstract
Description
Claims
Application Information

- R&D
- Intellectual Property
- Life Sciences
- Materials
- Tech Scout
- Unparalleled Data Quality
- Higher Quality Content
- 60% Fewer Hallucinations
Browse by: Latest US Patents, China's latest patents, Technical Efficacy Thesaurus, Application Domain, Technology Topic, Popular Technical Reports.
© 2025 PatSnap. All rights reserved.Legal|Privacy policy|Modern Slavery Act Transparency Statement|Sitemap|About US| Contact US: help@patsnap.com