High-temperature-resistant viscosity-reduction filtrate reducer for drilling fluid and preparation method of filtrate reducer
A filtrate reducer and high temperature resistance technology, which is applied in the field of oil drilling, can solve the problems of high cost, unsatisfactory viscosity reduction effect, unfavorable large-scale use in industrial production oil fields, etc., and achieve low cost, good viscosity reduction effect, and increased temperature resistance effect of ability
- Summary
- Abstract
- Description
- Claims
- Application Information
AI Technical Summary
Problems solved by technology
Method used
Image
Examples
Embodiment 1
[0049]Take 75 parts of acrylic fiber waste, cut it into pieces, add it to 1000 parts of water together with 30 parts of sodium hydroxide, raise the temperature to 90°C under stirring, and react for 3 hours; cool down to 85°C, add 30 parts of nitric acid with a concentration of 20wt% React with 40 parts of hydrogen peroxide at 90°C for 2 hours; add 80 parts of sodium hydroxide, 300 parts of lignite, 20 parts of sodium metabisulfite and 25 parts of formaldehyde, and react at 95°C for 2 hours; cool down to 70°C, add 10 parts of seven Ferrous sulfate in water, react for 20 minutes; discharge, dry and crush to obtain.
[0050] Take the anti-high temperature viscosity reducing fluid loss reducing agent prepared by the method of Example 1, and investigate its performance, and the results are shown in Table 1.
[0051] Table 1
[0052] project
Embodiment 2
[0053] Example 2: Take 120 parts of acrylic fiber waste, cut it into pieces, add it and 40 parts of potassium hydroxide to 1000 parts of water, raise the temperature to 95 °C under stirring, and react for 4 hours; cool down to 80 °C, add 50 parts of the concentration of 20wt % hydrochloric acid and 45 parts of hydrogen peroxide, heat up to 90°C for 3 hours; add 100 parts of sodium hydroxide, 350 parts of lignite, 25 parts of sodium bisulfite and 30 parts of formaldehyde, react at 95°C for 2 hours; cool down to 80°C , add 15 parts of ferrous sulfate heptahydrate, react for 30 minutes; discharge, dry and pulverize to obtain.
[0054] Take the anti-high temperature viscosity reducing fluid loss reducing agent prepared by the method of Example 2, and investigate its performance, and the results are shown in Table 2.
[0055] Table 2
[0056] project
Embodiment 3
[0057] Example 3: Take 160 parts of acrylic waste silk, cut it into pieces, add it and 45 parts of sodium hydroxide to 1000 parts of water, heat up to 88°C under stirring, and react for 2.5h; cool down to 85°C, add 55 parts of 20wt% of sulfuric acid and 45 parts of hydrogen peroxide, heated to 95°C for 2 hours; added 105 parts of potassium hydroxide, 400 parts of lignite, 30 parts of sodium sulfate and 40 parts of formaldehyde, reacted at 90°C for 3 hours; cooled to 60°C, Add 12 parts of ferrous sulfate heptahydrate, react for 15 minutes; discharge, dry and pulverize to obtain.
[0058] Get the anti-high temperature viscosity reducing fluid loss reducing agent prepared by the method of Example 3, investigate its performance, the results are as shown in table 3:
[0059] table 3
[0060] project
PUM
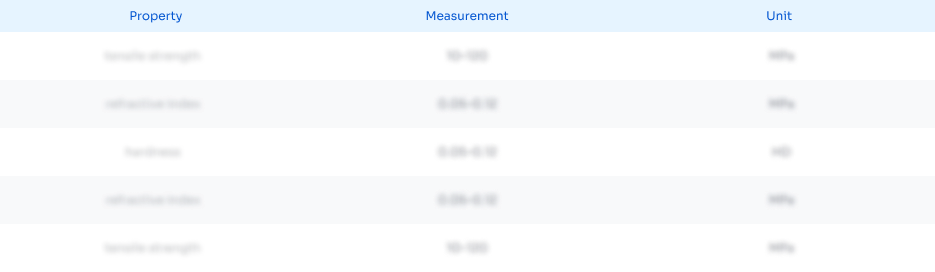
Abstract
Description
Claims
Application Information

- R&D
- Intellectual Property
- Life Sciences
- Materials
- Tech Scout
- Unparalleled Data Quality
- Higher Quality Content
- 60% Fewer Hallucinations
Browse by: Latest US Patents, China's latest patents, Technical Efficacy Thesaurus, Application Domain, Technology Topic, Popular Technical Reports.
© 2025 PatSnap. All rights reserved.Legal|Privacy policy|Modern Slavery Act Transparency Statement|Sitemap|About US| Contact US: help@patsnap.com