High temperature resistant anticorrosive paint and preparation technology thereof
An anti-corrosion coating, high heat-resistant technology, applied in the direction of anti-corrosion coatings, epoxy resin coatings, coatings, etc., can solve the problems of thin coatings, easy softening, cracks, thin coatings, etc., to achieve the goal of coating Thick layer and good flexibility, reduced construction cost, and high anti-corrosion performance
- Summary
- Abstract
- Description
- Claims
- Application Information
AI Technical Summary
Problems solved by technology
Method used
Image
Examples
Embodiment 1
[0039] A gray high heat-resistant anti-corrosion coating:
[0040] The specific composition and content of the main agent are as follows:
[0041] Novolac epoxy resin F-51: 300 grams
[0042] Xylene: 58.8 grams;
[0043] Butanol: 38.4;
[0044] Heavy aromatics: 21.6 grams;
[0045] Titanium dioxide 25.00g
[0046] Carbon black 0.5g
[0047] Body Pigment:
[0048] Ultrafine barium sulfate: 220 grams
[0049] Talcum powder 600 mesh: 80 grams
[0051] Additives include:
[0052] Anti-sedimentation agent 200x: 10 grams
[0053] Dispersant 301: 6 grams
[0054] Anti-sagging agent HI-1058: 50 grams
[0055] The raw materials of curing agent are:
[0056] Xylene: 140 grams;
[0057] n-Butanol: 91.5 grams;
[0058] Heavy aromatics: 51.48 grams;
[0059] Modified aliphatic curing agent 2280: 714 grams
[0060] The preparation process of above-mentioned coating is as follows:
[0061] 1. The preparation process steps of the main ingredie...
Embodiment 2
[0070] A red iron oxide high heat-resistant anti-corrosion coating:
[0071] The specific composition and content of the main agent are as follows:
[0072] Novolac epoxy resin F-51: 200 grams
[0073] Xylene: 49 grams;
[0074] n-Butanol: 32 grams;
[0075] Heavy aromatics: 18 grams;
[0076] Iron oxide red: 30 grams
[0077] Body Pigment:
[0078] Ultrafine barium sulfate: 200 grams
[0079] Talcum powder 600 mesh: 50 grams
[0080] Mica powder: 100 grams
[0081] Additives include:
[0082] Anti-sedimentation agent 200x: 20 grams
[0083] Dispersant 301: 1 g
[0084] Anti-sagging agent HI-1058: 30 grams
[0085] The raw materials of curing agent are:
[0086] Xylene: 98 grams;
[0087] n-Butanol: 64 grams;
[0088] Heavy aromatics: 36 grams;
[0089] Modified aliphatic curing agent 2280: 600 grams.
[0090] 1. The preparation process steps of the main ingredient:
[0091] 1) Ingredients: Stir the following materials evenly in order for ingredients: 170 gram...
PUM
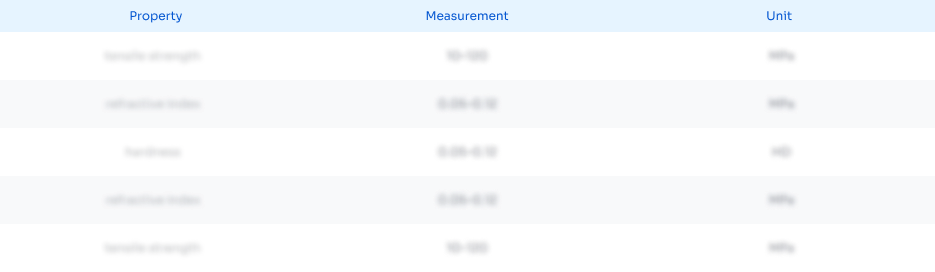
Abstract
Description
Claims
Application Information

- R&D
- Intellectual Property
- Life Sciences
- Materials
- Tech Scout
- Unparalleled Data Quality
- Higher Quality Content
- 60% Fewer Hallucinations
Browse by: Latest US Patents, China's latest patents, Technical Efficacy Thesaurus, Application Domain, Technology Topic, Popular Technical Reports.
© 2025 PatSnap. All rights reserved.Legal|Privacy policy|Modern Slavery Act Transparency Statement|Sitemap|About US| Contact US: help@patsnap.com