Production line of multi-color patterned roller-coated steel plate
A patterned roller, color steel plate technology, applied in general parts of printing machinery, cleaning methods using liquids, other manufacturing equipment/tools, etc.
- Summary
- Abstract
- Description
- Claims
- Application Information
AI Technical Summary
Problems solved by technology
Method used
Image
Examples
Embodiment 1
[0036] Such as Figure 4 As shown, the present embodiment provides a production line for roll-coated color steel plates ( figure 1 It is a flow chart of color steel plate production using the production line provided in this embodiment), including the following equipment: uncoiler 1, used to uncoil the crimped steel strip, and trim the steel strip; sewing machine 2, used to The front and rear steel strips after uncoiling of the uncoiler 1 are connected together to ensure the continuity of the process after replacing the steel coils; the first tension roller 3 is used to make the steel strips stitched by the sewing machine 2 run smoothly; the entrance looper 4. It is used to ensure that the process section does not stop when the uncoiler 1 is uncoiled and the sewing machine 2 is stitched; the second tension roller 5 is used to make the steel strip wound out of the inlet looper 4 run smoothly; The machine 6 is used for corona treatment of the steel strip; the third tension roll...
Embodiment 2
[0044] Such as figure 2 As shown, the present embodiment provides a roll coating device assembly 8 used in Embodiment 1, including a feeding device 81 for providing coating; a suction roller 82, whose peripheral surface is connected with the feeding device 81, The peripheral surface has a plurality of depressions that form image areas when filled with the paint; the rubber coating roller 83, whose peripheral surface is connected with the suction roller 82, is used to accept the paint in the coating process. The image area formed on the roller 83, and transfer the image area to the steel plate; the first scraper 84, installed on the first scraper bracket, contacts with the suction roller 82 at a specific angle, and is used to scrape off the image area. the paint outside the image area of the suction roller 82; and the second scraper 85, installed on the second scraper bracket, is in contact with the coating roller 82 at a specific angle, and is used to scrape off the rubber ...
Embodiment 3
[0049] This embodiment provides a kind of servo control system for the roller coating color steel plate production line in embodiment 1, comprises, PLC control module, and described PLC control module has collector, is used for collecting the roller of each roller of the first roller coating unit diameter and process speed data, the PLC control module also has a calculator, and the calculator is used to calculate the theoretical roll surface line speed of each roll according to the process speed and the roll diameter of each roll (the specific calculation method is: theoretical speed = process speed / W*roller diameter), theoretical roll surface speed=theoretical rotating speed*roller diameter*W), so that the theoretical roll surface speed of each roll is consistent with the process speed, and the calculated theoretical roll surface line of each roll The speed signals are respectively output, and the PLC control module also includes a comparator; the servo control module has an ...
PUM
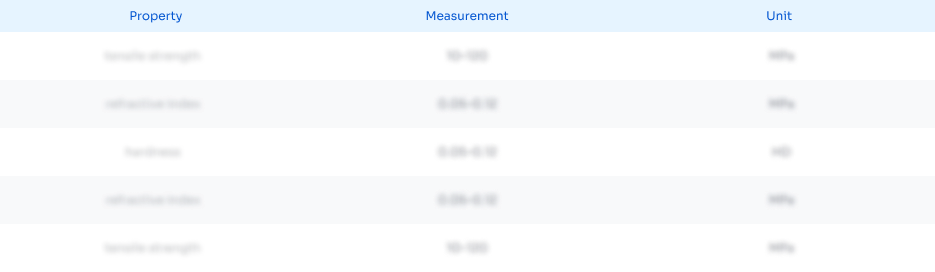
Abstract
Description
Claims
Application Information

- R&D Engineer
- R&D Manager
- IP Professional
- Industry Leading Data Capabilities
- Powerful AI technology
- Patent DNA Extraction
Browse by: Latest US Patents, China's latest patents, Technical Efficacy Thesaurus, Application Domain, Technology Topic, Popular Technical Reports.
© 2024 PatSnap. All rights reserved.Legal|Privacy policy|Modern Slavery Act Transparency Statement|Sitemap|About US| Contact US: help@patsnap.com