Method for carrying out progressive precision extrusion forming of thin-shelled parts with internal and external teeth based on generating method
A technology of extrusion forming and internal and external teeth, which is applied in the field of extrusion forming, can solve the problems of irregular deformation of the toothed part of the parts, expensive imported equipment, and no manufacturer seen, so as to reduce processing difficulty and reduce power. , the effect of high unit pressure
- Summary
- Abstract
- Description
- Claims
- Application Information
AI Technical Summary
Problems solved by technology
Method used
Image
Examples
Embodiment Construction
[0024] As an embodiment of the present invention, such as Figure 1 to Figure 3 As shown, a method for progressive precision extrusion forming thin shell parts with internal and external teeth based on the generation method, including the following steps:
[0025] Step A: Make the main shaft mold 4 and the pressure wheel mold 5, the surface of the main shaft mold 4 is provided with a number of teeth for forming the internal teeth of the thin shell parts with internal and external teeth, and the surface of the pressure wheel mold 5 is provided with a number of teeth for forming Gear teeth with external teeth of thin shell parts with internal and external teeth;
[0026] Step B: Set main shaft 1, synchronous main shaft 2, synchronous pinch roller shaft 3, pinch wheel radial feed shaft and pinch wheel axial feed shaft, main shaft 1 drives synchronous main shaft 2, synchronous main shaft 2 drives synchronous pinch shaft 3, and the main shaft mold 4 is installed on the main shaft ...
PUM
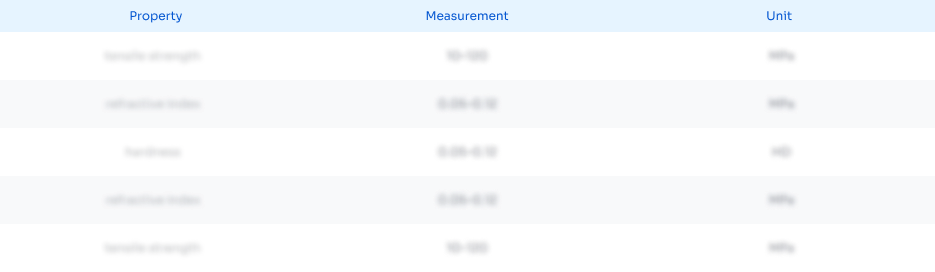
Abstract
Description
Claims
Application Information

- R&D
- Intellectual Property
- Life Sciences
- Materials
- Tech Scout
- Unparalleled Data Quality
- Higher Quality Content
- 60% Fewer Hallucinations
Browse by: Latest US Patents, China's latest patents, Technical Efficacy Thesaurus, Application Domain, Technology Topic, Popular Technical Reports.
© 2025 PatSnap. All rights reserved.Legal|Privacy policy|Modern Slavery Act Transparency Statement|Sitemap|About US| Contact US: help@patsnap.com