Argon bleaching and dyeing technology of acrylic yarn
A yarn and acrylic fiber technology, which is applied in the direction of bleaching products, textiles, papermaking, dry-cleaning fiber products, etc. It can solve the problems of not being able to maintain the soft and full hand feel of the yarn, not being able to fully oxygen bleach the acrylic fiber fabric, and affecting product quality. Achieve high-quality bleaching effect, improve product quality, and improve yarn whiteness
- Summary
- Abstract
- Description
- Claims
- Application Information
AI Technical Summary
Problems solved by technology
Method used
Examples
Embodiment Construction
[0012] The present embodiment will be further described in detail below.
[0013] A kind of acrylic yarn argon bleaching dyeing process of the present invention comprises the following steps:
[0014] (1), first place the acrylic yarn in water, and then add additives sequentially, the additives are chelating dispersant, the dosage is 1g per liter of water, oxalic acid, the dosage is 1g per liter of water, sodium chlorite , the consumption is 1g per liter of water, sodium nitrate, the consumption is 0.5g per liter of water, sodium nitrate, the consumption is 1g per liter of water; Do not add ingredients in disorder, so as to affect product quality;
[0015] (2) Raise the temperature of the aqueous solution with the additives added, by 1°C every 1 minute, when the temperature rises to 95°C, keep it warm for 30 minutes, and then remove the aqueous solution;
[0016] (3), washing the acrylic yarn after removing the aqueous solution in hot water, and then draining;
[0017] (4) ...
PUM
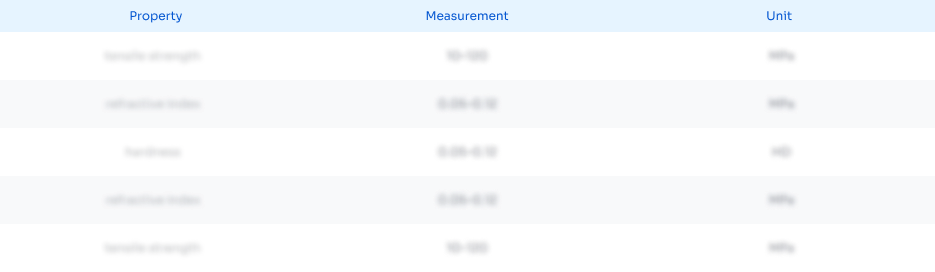
Abstract
Description
Claims
Application Information

- Generate Ideas
- Intellectual Property
- Life Sciences
- Materials
- Tech Scout
- Unparalleled Data Quality
- Higher Quality Content
- 60% Fewer Hallucinations
Browse by: Latest US Patents, China's latest patents, Technical Efficacy Thesaurus, Application Domain, Technology Topic, Popular Technical Reports.
© 2025 PatSnap. All rights reserved.Legal|Privacy policy|Modern Slavery Act Transparency Statement|Sitemap|About US| Contact US: help@patsnap.com